Monday 30 November 2020
Time slots: 12:30 PM CET | 8:30 PM CET | 4:30 AM+1 CET
Duration: 05:15:00
A new approach to Composite Design
The use of Carbon Fibre Reinforced Plastic (CFRP) materials is common practice today in many industrial fields (such as aeronautics, automotive, space, railways, and sports), but, unfortunately, design methodologies have remained practically unchanged since the world first began appreciating their potential benefits in the early 1970s.
The design and structural optimization of these types of materials is strongly influenced by the huge number of variables involved. In fact, while the customization of the staking sequences can generate very efficient structures, on the other hand it leads to remarkably complex mathematical models and expensive structures.
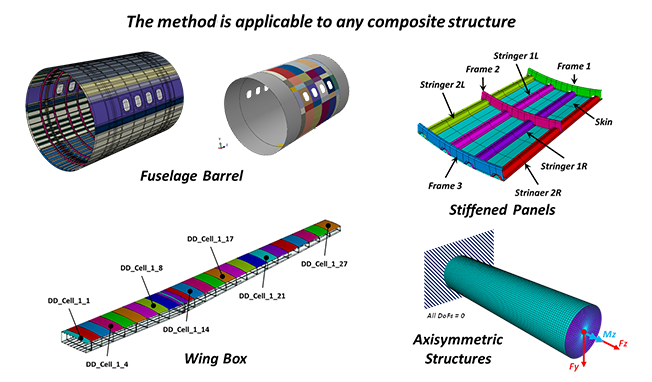
In order to limit the number of variables and, above all, to preserve the knowledge acquired in the past decades, the possible variations of the ply-angle are basically limited to four: 0 °, 90 °, 45 °, -45 °. The laminates with such ply-angles are the so-called QUAD laminates. The use of only these ply-angles, associated with the so-called rules of good composite design, leads to considerable manufacturing complexity and therefore to high manufacturing costs.
In the last few years, thanks to research led by Stanford University and Prof. Tsai, it has been shown that a new family of laminates could not only greatly simplify the design phase, but also significantly reduce manufacturing costs. This laminate family has been named Double-Double. As the name already suggests, each laminate is identified by only two ply-angles, and, more importantly, can be characterized by a single mechanical property, Tsai’s Modulus, just like classic isotropic materials.
AGENDA
Keynote Speaker: Stanford University, Department of Aeronautics & Astronautics | Stephen W. Tsai
A paradigm shift in composites design from quad to double-double
Department of Engineering, University of Campania "Luigi Vanvitelli", Italy | Aniello Riccio
Double-Double for Aircraft Structures
C.I.R.A. Italian Aerospace Research Centre, Italy | Francesco Di Caprio
An Ansys based automatic tool for design novel Double-Double Composite Structure
Department of Structural Engineering Federal University of Minas Gerais, Brazil | Carlos Alberto Cimini Jr
Simplifying carbon/epoxy composite laminate design
Universidade do Porto – Faculdade de Engenharia, Porto, Portugal | Albertino Arteiro
Reduced material allowables with Tsai’s modulus – DD case study
NASHERO s.r.l, Italy | Naresh Sharma
Composite Aircraft Certification for Double Double Structures
Department of Mechanical Engineering, University of California, Berkeley, USA | Zilan Zhang
Machine Learning for Accelerating Double-Double Laminates Simulations
Keynote Speaker
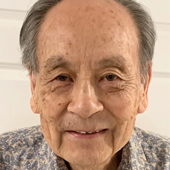
Stanford University, Department of Aeronautics & Astronautics | Stephen W. Tsai
A paradigm shift in composites design from quad to double-double
The emergence of double-double in [± Φ / ± Ψ] to replace traditional quad of 0, ±45, 90. Is based on a number of innovative steps in the modelling of composite laminates. For double-double, Tsai’s modulus is the beginning the master ply and one-constant stiffness. This is followed by homogenization made possible with only 4- instead of normally 20-ply quad laminate building blocks. Homongenized laminates are naturally symmetric, and ply drop can be in singles, rather than symmetric pairs for quad. Lightly loaded areas can have reduced thickness that quad cannot do without changing laminate properties. There is no stacking sequence effect on DD while for quad, there are hundreds and thousands of stacking permutation making not only optimization impossible, but also uniqueness in question. With homogenization DD laminates can be laid up in along 1-axis. Ply drops can be located on the exterior surfaces. In the interior of laminates, it is with resin-pockets, fiber breaks, and ply movement that causes wrinkles commonly encountered with quad laminates. Thus faster, less error prone layup, and defects free interior make DD laminates lower cost and higher quality. One DD can cover the entire domain of a component with taper strength and/or buckling based taper. There will be no blending issue common with quad laminate. Hard point and repair can use the same in-family DD so the patch will not cause discontinuity stresses. DD is field-based with continuous variable angles whereas quad is discrete and discontinuous. Cannot interpolate or extrapolate, and have derivatives. It is the difference between day and night. DD in time will be the standard and composites laminates and structures will be more competitive. It is really like an orthotropic aluminum. As easy to design and manufacture as aluminum except it weight less than 50 percent. While complete data on DD are forthcoming, there are no indications that they are weak in any aspect that would include damage to damage toleration, BVID, and fatigue. It is a new dawn and engineers should be pleased to be armed with a better approach to make composites more competitive.
Curriculum
Stephen W. Tsai is Professor Research Emeritus, Aeronautics and Astronautics at Stanford University and Chief Engineer at Think Composites.
Research by Stephen W. Tsai led to several formulas and failure criteria in composite materials bearing his name, which have become common practice in composites design and implemented in number of commercial software. These criteria have also become standard textbook material and been referred in most of the research articles in design and analysis of composite structures.
There are several awards at international conferences on composite materials to honor his contributions in the field, as well as several book witnessing his research interests and pioneer approach, as his last publication in time “Composite Double-double and Grid/skin Structures”, with Naresh Sharma, Albertino Arteiro, Surajit Roy, and Robert Rainsberger, Stanford Composites Design Group, 2019
Process and product development of composite materials that may lead to improved design practice and commercialization. His current interests include composite behavior as affected by static, creep and fatigue loading, and products like composite rotors for flywheel systems. Emphasis is on the design, manufacturing and evaluation of the performance and cost. Methodology and supporting software to provide safe service of 30 years under combinations of loads, temperatures and moisture. Also pioneering spreadsheet based composites design tools. His continuing projects (since 2007) include online composites design workshops, which provide intensive, live training to thousands of around the world.
Technical session
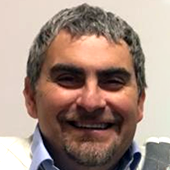
Department of Engineering, University of Campania "Luigi Vanvitelli", Italy | Aniello Riccio
Double-Double for Aircraft Structures
The definition of lightweight solutions for aeronautic components has become in the last decades one of the key aspects in their design process. The use of composites structures has allowed to reach weight savings of aeronautic components never reached in the past. However, the traditional composite designs based on the adoption of quad laminates, have shown many limitations in terms of layup and weight optimization, providing often over-dimensioned solutions not fully realizing the potential of composite materials. In order to step up the composite design, Double-Double laminates can be adopted which can guarantee, with considerably thinner and more homogenized layups, the same level of strength obtained with quads. The double-double concept is relatively new and both experimental and numerical investigations need to be carried out to improve the actual knowledge on DD laminate stiffness and strength characteristics. In particular, suitable numerical tools need to be developed to promote effective design solutions. In order to show the real DD potential, in the frame of the presented work, a numerical DD design automated tool, able to improve the weight saving characteristics of composite components, is introduced and applied to considerably improve the design of significant aeronautic components.
Curriculum
Aniello Riccio defended his PhD in Aerospace Science and Technologies, at the Second University of Naples in 1999. PhD thesis subject: development of numerical tools for delamination growth in impacted composite panels. Thanks to the PhD thesis work, he was awarded in 2000 (Brussels) with the first edition of “the Pratt & Whitney - EREA Award”. From 2000 to 2010, Aniello Riccio worked as researcher in Capua (Italy) at C.I.R.A. (Italian Aerospace Research Center) as a member of the group of Structures and Materials. The main focus of his research work was the modelling of damage mechanics in composite materials and structures. From 2006 he has been chairman of several European, national Italian and regional Research Projects: GARTEUR AG-34 (2012-2015) (Damage repair with Composites). GARTEUR AG-32 (2006-2009) (Damage Growth in Composites) and GARTEUR AG-31 (2006-2009) – DAMOCLES III (Damage Management of Composite Structures for Cost Effective Life Extensive Service). MACMES phase I (2009-2010) (Damage Management of Aircraft Composite Structures Monitored by Embedded Sensors) in the frame of the National Military Research Programme. From 2003, Aniello Riccio is Member of the GARTEUR (Group for Aeronautical Research and Technology in EURope) Structures and Materials Group of Responsibles (chairman from 2008-2011.
In 2010 he joined University of Campania “Luigi Vanvitelli” (Former Seconda Università degli Studi di Napoli) first as researched then as Full Professor of Aerospace Structures and construction courses. He is author of more than one hundred papers listed in SCOPUS and he is reviewer, editorial member and associate editor for several international Journals and books and referee for international and national Research Projects.
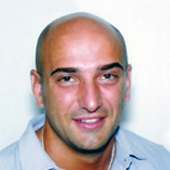
C.I.R.A. Italian Aerospace Research Centre, Italy | Francesco Di Caprio
An Ansys based automatic tool for design novel Double-Double Composite Structure
Double-Double laminates have been demonstrated to be, generally, stronger and lighter than legacy quads laminates. The related results regarding the introduction of double-double laminates leads to a significant change in the design techniques of structures made in fibre reinforced plastic materials. The analysis tools used up to now for design process are still unable to benefit from the high potential that this type of laminates could provide. The proposed DD-Design Tool enables to convert an originally designed Quad composite structure to an efficient DD composite structure in the simplest way. The DD-Design Tool uses a fully automated iterative procedure interfacing FE models with the Direct Conv Tool in order to generate and verify the best DD layup for any composite structure. The updated stress distributions, evaluated by means of the FEM analyses, are provided, iteratively, to the Direct Conv Tool, in order to determine the best DD angles combination satisfying the stiffness requirements of the input tentative (quad) configuration. Strength requirements are taken into account to perform a weight optimization and to deliver a final optimized resulting DD configuration. The tool generates alternative DD configurations (tapered), which are able to simplify the manufacturing process allowing a relevant time and cost saving.
Curriculum
Francesco di Caprio, is an aerospace engineer with a specialization in structure analysis. He achieved the PhD in Aerospace Sciences and Technologies, with a thesis on the development of fast numerical procedures to be used in preliminary stages of damage tolerant composite structures design.
He has been working with CIRA (Italian Aerospace research centre) since 2011, and in particular he works in in the Airframe Design and Dynamic Laboratory, under Structure and Material Division. His main research activities focus to airframe structural design, numerical methods, structural optimization, design methods for composite structures.
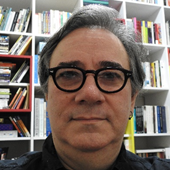
Department of Structural Engineering
Federal University of Minas Gerais, Brazil | Carlos Alberto Cimini Jr
Simplifying carbon/epoxy composite laminate design
Carbon/epoxy composite laminate design usually relies in a large set of parameters, which are defined as properties of the material. Using the ply as the building block, designers need to know four independent elastic constants (Ex , Ey , Gxy , and νxy) plus a set of five or more strength allowables, depending on the failure criterion to be chosen. In the case of the more traditional failure criteria, five strength allowables are required (X , X’ , Y , Y’ and S). A novel approach is proposed, based on only three parameters to define all those properties: one for the elastic constants and two for the failure criterion. The elastic constants can be derived based on the invariant master ply theory and the Tsai’s modulus using just the Young’s modulus in the fiber direction (Ex). This single parameter is sufficient to define the Tsai’s modulus (trace of the ply stiffness matrix) which is invariant and thus considered a material property itself. Together with the master ply stiffness matrix derived for the carbon/epoxy class of composite materials, the particular stiffness matrix can be obtained for any material of this class. This concept can be extended from the case of plane stress ply, to plane strain thick ply and fully 3D bulk orthotropic material. Failure analysis is performed in the strain domain, using either two (X and X' or their corresponding strains) or, more conservatively, one parameter based on whichever is smaller. The unit circle is enclosed by the last ply failure (LPF) omni-envelope. Even more conservatively, it can be considered the Nettle’s circle, limiting the design allowable failure strain to 4,000 microstrain, with no need for a failure parameter. Nettle’s circle cover damage tolerance and virtually make composites an isotropic material, regarding the required constants: just one parameter is needed for design.
Curriculum
Experienced aeronautical engineer, professor and researcher, with focus on structures and composites, currently holding the position of Professor at Federal University of Minas Gerais (UFMG) in Brazil. Graduated as Mechanical Engineer specialized in aerospace structures in 1984 at UFMG. Worked as aircraft structures analyst engineer at EMBRAER (Brazilian Aircraft Manufacturer). Obtained his Master's in Structural Engineering in 1992 at UFMG and his Ph.D. in Aeronautics and Astronautics in 1997 at Stanford University, under the supervision of Prof. Stephen W. Tsai. Worked in the Advanced Ducted Propulsor program at Pratt & Whitney in the summer of 1995. Visiting scholar at Stanford University (2007-2009) and at the Royal Institute of Technology, KTH (2016-2017). Works on composites failure and life prediction, structural health monitoring, stress analysis, fatigue and fracture. Also conducts multidisciplinary studies in modeling biological systems and structures.
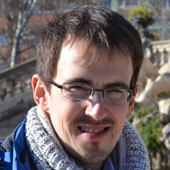
Universidade do Porto – Faculdade de Engenharia, Porto, Portugal | Albertino Arteiro
Reduced material allowables with Tsai’s modulus – DD case study
Obtaining material allowables from testing alone is resource intensive and beyond the means of all except the largest aircraft producers. In addition to the inefficiency of the current design and certification procedures of composite structures, which is a sufficient motivation for the development of new composite qualification methods for aircraft design, the fact that these procedures are based on legacy laminate configurations strongly limits the introduction of new materials and design concepts, such as the double-double (DD) technologies. The understanding of the physical behavior of CFRPs and the use of precise relationships between their material properties has not only the potential to make design and certification more affordable, but it also opens-up new possibilities for application of advanced materials and novel laminate configurations. Tsai’s modulus– the trace of the in-plane stiffness matrix – and omni envelopes in combination with fracture mechanics concepts establish the required relationships towards efficient and reliable certification procedures for CFRP structures, which are independent of the material form and laminate configuration. In a case study involving DD laminates manufactured by NASHERO s.r.l., the plain and open-hole tension data is first identified experimentally from a DD [±15/±60] laminate. Using Tsai’s modulus, one laminate only (no unidirectional ply data) is necessary for generation of the allowables. Then, an omni failure criterion, a fracture mechanics model and a Finite Fracture Mechanics criterion is used to extrapolate the mean and B-values for other laminates. Tests conducted on a DD [±0/±50] laminate are used for validation. It is impressive how the mean values extrapolate so well from one laminate to the other. On the other hand, the B-values are conservative, mainly because the DD [±15/±60] laminate shows more scatter in the test results. Thanks to the understanding of the physical behavior and relationships between material properties of CFRPs, as well as other advanced composites, the new possibilities for more efficient design and certification are endless. This has the great potential of making composite aircraft structures more affordable and competitive, and embracing such philosophy can lead to the next game changer of this industry.
Curriculum
Albertino Arteiro received a Master's Degree in Mechanical Engineering - Specialisation in Structural Engineering and Machine Design - from the Faculty of Engineering - University of Porto in 2012, and a Doctoral Degree in Mechanical Engineering (cum Laude) from the same University in 2016, during which he was a Visiting Student Researcher at the Department of Aeronautics and Astronautics of Stanford University. He was awarded the Best PhD Thesis by the Portuguese Association of Theoretical, Applied and Computational Mechanics (APMTAC). Albertino Arteiro was appointed Assistant Professor at the Materials and Technological Processes Group of the Department of Mechanical Engineering (DEMec) of the Faculty of Engineering – University of Porto in 2019. He is currently a member of the ECCOMAS Young Investigators Committee. His research interests include material modelling at different length-scales, design and analysis of composite systems based on new concepts, and composites manufacturing.
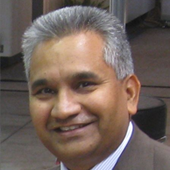
NASHERO s.r.l, Italy | Naresh Sharma
Composite Aircraft Certification for Double Double Structures
Due to their material properties and behaviour, composite materials, esp. carbon fibre reinforced plastics (CFRP) are highly suited for use in applications where low structural mass is desirable. Carbon composites provide:
1. High specific strength
2. High specific stiffness
3. High corrosion resistance
4. Shape conformance to a structural load spectrum
5. Aerodynamic cleanliness
6. High fatigue strength and toughness
7. Capability to design high energy dissipation structures for crashworthiness
Aircraft certification is a means to prove that a structure, designed, built, operated and maintained using the certified processes would be safe in its entire mission profile for the lifetime of its certification. Historically, the Federal Aviation Administration (FAA) in the USA and European Aviation Safety Agency (EASA), in Europe and many other countries are the two main agencies in the world that have set forth the standards for aircraft certification that are currently used worldwide. Once an aircraft is certificated, its fleet’s operational experience is recorded and such records have been analyzed by the FAA and EASA generating a vast database of the aircraft’s operational and maintenance life.
The experience with metal aircraft certification has pointed to some challenges in the certification of composite aircraft, due to which starting in the 1970’s to 1990’s significant work was carried to understand the predictability of composite aircraft’s safety. Early composite aircraft designs used some thumb-rules, guided by engineering opinion as opposed to analytical understanding one of which is the 10% rule, which says that at least 10% of fibres in any structure should be in one of the 0/90/+-45 deg angles. Many of these thumb-rules are still followed in the industry. Variability in composite constituents such as epoxies, their chemical composition and structural behaviour, fibres and the production techniques of composites has historically ebbed on the advantage of composite materials. Lack of standardized data and capability of reproducing that data in production conditions is another issue marring the work till the late 1990’s.
In the 2000s, significant investment by companies in production techniques, standardization of material systems, development of new fibres etc, has helped this aspect. Today, there is a public database by NCAMP at Wichita State University, standardized materials which are accepted by FAA and EASA. The old composite design philosophies, in absence of their theoretical basis, such as the 10% rule, still are the norm.
The recent work by Prof. Tsai and his group has analytically proven that composite orthotropic materials have an elastic property, a constant, Tsai’s Modulus. Tsai’s modulus is unique for a material system and fibre combination and can, therefore, be used to generate the material-behaviour of any orthotropic carbon composite from a single test data.
In this presentation, we’ll discuss the differences in the behaviour of carbon composite structures compared to those of metal. The current certification mechanisms for aircraft made in metal as compared to composites. We’ll also touch on the exciting new Double Double technologies developed by Prof. Tsai’s group and their impact on aircraft design, certification, optimization, production and maintenance.
Curriculum
Naresh Sharma is the CEO and Founder of NASHERO, a light aircraft manufacturer out of North Italy. NASHERO designs, develops, produces and sells carbon composite aircraft. With the impending AS9100 certification, they plan on supplying larger OEMs with technology, composite and complex precision machined metal parts. Since 2008, Naresh is an ASTM member and an active contributor to the ASTM’s aviation standards including those for General Aviation.
Naresh earned a PhD in Aerospace Engineering and Computer Sciences from the Delft University of Technology in 1997, a Master’s in Aeronautical Engineering from the Indian Institute of Technology (IIT), Kanpur (1987-1989), and a Bachelor’s in Mechanical Engineering from IIT, Kanpur (1982-1986).
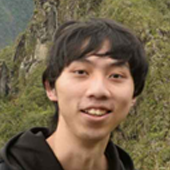
Department of Mechanical Engineering, University of California, Berkeley, USA | Zilan Zhang
Machine Learning for Accelerating Double-Double Laminates Simulations
For decades, composite materials have been widely used in many fields such as aerospace, automobile and electronics. In order to manufacture lighter laminates with less cost, optimization is conducted, which often requires running expensive multi-physics simulations. One limitation of simulation lies in that it is time consuming, involving solving thousands of differential equations, leading to inefficient optimization processes. One method to potentially improve the efficiency of optimization is the application of machine learning.
In this project, machine learning is applied to simulation to achieve fast and highly accurate prediction of composite simulation results. The training data are derived from a parametrized 2D wing-shaped Double-Double (DD) composite model. Input variables include geometry parameters, material properties, and force parameters. One of the geometry inputs is the stacking sequence. Conventional QUAD laminates have four fixed ply-angles: 0^∘, 90^∘, 45^∘ and -45^∘. It is difficult to define an organized digital input that constructs various stacking sequences. DD composites reduce the complexity by having only two ply-angles [±ϕ/±ψ] which fully define the laminate. The two angles will be used as the stacking sequence inputs. The major outputs include the stress and strain of nodes and can be further visualized. The trained data-driven algorithm will yield a considerable decrease in optimization time, leading to less computational cost and more composite design choices. The project is divided into three stages, data collecting, training, and testing. Currently data is gathered using ANSYS Mechanical APDL. The prewritten script can run parameterized simulations and store output data. Various training methods will be applied to the data, together with testing that verifies the accuracy of training results. This model of machine learning on DD composite simulations can be easily extended to cases such as 3D structures or thermal simulations, expanding the design space to composite material and structure designs in aerospace structure design and automobile industries.