Tuesday 1 December 2020
Time slots: 10:00 AM CET | 6:00 PM CET | 2:00 AM+1 CET
Duration: 02:40:00
Energy, Oil & Gas Session | Part 1
AGENDA
Keynote Speaker: ASSESS Initiative | Joe Walsh
ASSESS: Leading the Simulation Revolution
Casappa spa | Sara Bonati
CFD Simulation of an Axial Piston Pump with Ansys CFX
Bosch Thermotechnology | Yiğit Gürler
Modelling and Simulation of Environment Friendly Packaging Concept for Combi Boiler
Castel | Lorenzo Resmini
Multi-phase fluid-dynamic simulation in electric expansion valves for refrigeration and air conditioning applications
Eaton India Innovation Centre LLP | Shashank Mishra
Modified Lumped Modelling Approach for Simulation of Electrical Components in Switchgears
PETROLVALVES SPA | Simone Bosotti
Swing check valve seat-clapper dynamic structural impact simulation using Ansys Autodyn explicit solver
Fluids & Co | Vincent Soumoy
The right 1D - CFD choice for your digital transformation
SIMUNE Atomistics | Anna Kimmel
Multi-physics approach for materials modelling
Keynote Speaker
ASSESS Initiative | Joe Walsh
ASSESS: Leading the Simulation Revolution
The changing role of Engineering Simulation is really about business benefits. However, achieving those benefits and the Engineering Simulation market's associated growth is tempered due to the lack of expertise available. Business drivers are forcing a "simulation revolution" to overcome the expertise-based limitations restricting the expansion of Engineering Simulation applications.
The Simulation Revolution is about making Engineering Simulation widely available & appropriate to support improved decision-making throughout the entire life-cycle of engineered products and processes. We need a broad multi-industry initiative to raise awareness and develop/promote strategies to enable the Simulation Revolution.
The ASSESS (Analysis, Simulation, and Systems Engineering Software Strategies) Initiative was formed to bring together key players to guide and influence strategies for software tools for model-based analysis, simulation, and systems engineering.
This session will provide an update on the ASSESS Initiative completed and planned activities to support the Simulation Revolution.
Curriculum
Joe Walsh - CEO/Founder intrinSIM LLC - CEO/Co-Founder ASSESS Initiative LLC
Joe Walsh founded intrinSIM in late 2009 to enable rapid next-generation application development for engineering software, and he also co-founded the ASSESS Initiative in mid-2016 to significantly increase the usage and benefit of Engineering Simulation. Mr. Walsh brings over 40 years of experience, expertise, relationships, and collaborations in the CAE, CAD, interoperability, and component software industries. Before founding intrinSIM, He was the VP of Business Development for Simmetrix, where he was responsible for sales, marketing, and business relationships. Before joining Simmetrix, he was VP of Worldwide Sales for IronCAD LLC, VP of North American Sales for DS/Spatial and Spatial Corp., Partner and Founder of New Renaissance, President/CEO and co-founder of FEGS Inc. the North American subsidiary of FEGS, Ltd. of Cambridge UK, President/CEO of PAFEC Inc. the North American subsidiary of PAFEC Ltd. of Nottingham UK, Director of Engineering Applications for Clevenger Corporation and Mr. Walsh has almost ten years experience in engineering analysis positions specializing in CAD/CAE integration, CAE automation, and design optimization. Joe Walsh holds an Architectural Engineering degree from Milwaukee School of Engineering.
Technical session
Casappa spa | Sara Bonati
CFD Simulation of an Axial Piston Pump with Ansys CFX
Thanks to their compactness and efficiency, swashplate axial piston pumps are widely used as fluid power sources in fixed and mobile applications that require high pressure and variable flow rates. In order to guarantee high performances, reliability and reduced time-to-market, their development process requires more and more the use of advanced simulation tools.
With specific reference to fluid dynamic simulation, different approaches are available; nowadays, the most common one is still represented by the lumped parameter method (0D-1D models). The advantages of this approach are the fast computational time and the easiness to reach convergence, but some physical phenomena are inevitably simplified or even neglected at all. In this sense a three-dimensional approach is the most advanced and accurate method; nevertheless there are still considerable challenges to overcome before reach a comparable level of usability: CPU time and convergence issues, in order to solve complex transient analyses characterized by small clearances and high pressure drops.
In this work, a CFD model of fluid flow in an axial piston pump, working at high pressure, is presented. The presentation will show the workflow for the construction of the model in Ansys CFX and the model validation through quantitative comparison of predicted chamber pressures and fluid flows with those obtained with a validated 0-D model. Finally, an overview of phenomena related to spatial trajectory of oil jets inside the pump will be shown.
Curriculum
A motivated CAE Analyst with 3+ years of experience on hydraulic components design.
Experienced in product development. Focused on customer satisfaction and technology innovation. Skilled at problem solving and team working.
PROFESSIONAL EXPERIENCE
R&D Simulation Engineer at Casappa SpA 2017 – present
As a R&D engineer, my core activities include: Development of technical solutions in hydraulic field - Development of customized product in close
collaboration with customers - CAE analyses: optimization, FEM, CFD analyses, software development - Research activity
Graduate Research Fellow at Università degli Studi di Parma 2016 – 2017 | Topic: “Development of a thermodynamic lumped-parameter model for Wankel compressor”.
EDUCATION
Master’s Degree in Mechanical Engineering, Università degli Studi di Parma
Bachelor’s Degree in Mechanical Engineering, Università degli Studi di Parma
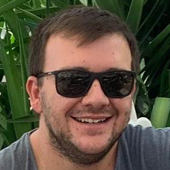
Bosch Thermotechnology | Yiğit Gürler
Modelling and Simulation of Environment Friendly Packaging Concept for Combi Boiler
The combi boiler is a heating appliance that is used for providing a heat power for central and domestic hot water lines. These type of devices are exposed to loads such as drop, vibration, temperature, and stack that may cause damage starting from production to end user. Drop is more pronounced when considering other damage factors in terms of the effect of damage and probability of occurrence. EPS is one of the commonly used packaging material to protect white goods and combi-type appliances from such damage mechanisms. However, with the environmental regulations that have come into effect in the European market, especially in the UK in recent years, restrictions are being made on disposable plastic-based materials. Therefore, environmentally friendly packaging material alternatives that can be used instead of EPS come to the fore.
In this study, a packaging concept with paper-based honeycomb material was designed for the combi boiler and numerical analysis of the drop test was performed using LS-DYNA software. The findings obtained from numerical analysis were compared for packaging concept designs realized with EPS and environmentally friendly packaging material. The energy absorbed by the packaging elements and the deformation levels transferred to the appliance were determined.In this context, by guiding the packaging system development process, design improvement suggestions were made. As a result, the appliance cost and time used for experimental testing are saved.
Curriculum
Yiğit Gürler was born on 29 December 1992 in Izmir, TURKEY. He received his BSc and MSc degrees from respectively the Department of Mechanical Engineering of CBU and Izmir Institute of Technology (IZTECH). Mr.Gurler is currently doing PhD in the Department of Mechanical Engineering of IZTECH under the supervision of Prof.Dr. Alper Taşdemirci and Prof.Dr. Mustafa Guden. At the same time, he is working as Hydraulic Module Design Engineer in the Research and Development Center of Bosch Thermotechnology. His main research topics include static / dynamic mechanical characterization and modelling of materials, finite element analysis of fiber reinforced thermoplastics.
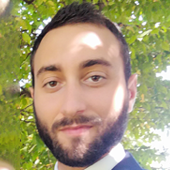
Castel | Lorenzo Resmini
Multi-phase fluid-dynamic simulation in electric expansion valves for refrigeration and air conditioning applications
Electric expansion valve (EEV) is one of the most important devices in refrigeration and air conditioning applications and it has the purpose of taking the refrigerant fluid from the condensing pressure to the evaporating pressure.
The aim of the present activity is the calculation of refrigerant capacity in order to populate Castel's EEV manual which allows the refrigeration equipment manufacturers to select the most suitable component for their applications.
An in-depth numerical investigation has been carried out with the suite ANSYS CFD and this led to geometrical modifications that allowed to reach the desired refrigerant capacity values and a better internal design of critical geometries. The main challenge of this numerical study was modelling the transition of the fluid phase from liquid to gas.
The low capacity values obtained with CAE technology have been experimentally verified by a refrigeration testing system owned by Castel’s laboratory.
Curriculum
After the degree in aeronautical engineering at Politecnico di Milano I started working as manufacturing engineer at UTC AEROSPACE SYSTEMS. This first experience allowed me to deal with a dynamic and innovative work environment and gave me the chance to deepen NADCAP program for the most common special processes used in the aerospace industry.
The second work experience was at MATTEI GROUP, a company which manufactures compressors. This period increased my knowledge in turbomachinery and in the rotary vane technology. The company where I have been working now is CASTEL, italian leading supplier of refrigeration and air conditioning components. My role as R&D Engineer is focused on new products desing, development of new technologies and laboratory activities. CASTEL provided me the great opportunity to widely deepen CAE technologies, this allowed me to become internal responsible both for CFD and FEM analysis.
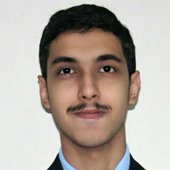
Eaton India Innovation Centre LLP | Shashank Mishra
Modified Lumped Modelling Approach for Simulation of Electrical Components in Switchgears
In electrical switchgears, heat generation due to electrical resistivity, eddy currents and contact resistance results in temperature rise. This temperature rise exceeding the allowable limits as prescribed in standards may lead to potential damage to electrical devices within the switchgear reducing its life and efficiency. In the recent times, there has been a tremendous impetus towards modelling of switchgears to reduce the design & development cycle time as the requirement of reduced footprint poses increased challenges to meet the thermal requirements.
A typical Low voltage switchgear consists of many electrical components such as busbars, ACBs, MCCBs, relays, contactors etc. Detailed modelling of switchgear systems along with these electrical components becomes difficult due to geometrical complexities and meshing constraints. Hence, general practice followed in industry is to model electrical components in full system modelling as lumped heat sources as per catalogues power loss data. This approach though computationally faster, jeopardizes the accuracy of temperature rise predictions as it doesn’t closely simulate the actual physics of heat interaction of the component with the neighboring environment in 3D simulations/modelling. Present work aims to develop a Modified Lumped Modelling approach that captures the distribution of heat dissipation from/within the component closer to reality without altering its interaction with the neighboring environment in 3D thermal simulations of full assembly. Experimental temperature rise test results of individual components is used to determine the distribution of heat loss from/within the component. Similar approach is then further extended to two or more components (e.g. MCCB and contactor), which are coupled in series in drawers of switchgear. This Modified Lumped Modelling approach when utilized in 3D modelling and simulation of complete switchgear system, results in improved accuracy without compromising computational time for different variations of switchgears based on Ingress protection, ambient conditions, ventilation systems for same combination of components inside a drawer. Simulation results for individual component, components coupled in series and switchgear system are validated with temperature rise tests. For individual component, the correlation coefficient is 0.98 and Absolute Average Deviation (AAD) is 5.1%; whereas for coupled systems, the correlation coefficient and AAD is found to be 0.96 and 10.79% respectively. For complete switchgear system the correlation coefficient and ADD are 0.93 and 5.84% respectively.
Curriculum
Shashank Mishra is an Engineer at Eaton India Innovation Center, Pune, India. His educational background includes Master’s in Thermal Engineering from Indian Institute of Technology, Madras and Bachelor’s in Mechanical Engineering from DIMAT, Raipur. He started his career in 2017 as Engineer in Eaton, Pune working on modelling and simulation of electrical switchgears. Currently he is working on Centre for digital prototyping and twins. He has 2 patents filed against his name.
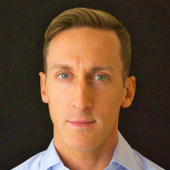
PETROLVALVES SPA | Simone Bosotti
Swing check valve seat-clapper dynamic structural impact simulation using Ansys Autodyn explicit solver
Swing check valve seat-clapper dynamic structural impact simulation due to pipe rupture of the upstream pipeline, by means of Ansys Autodyn explicit solver (free for mechanical enterprise license) instead of classical LS-Dyna explicit one (not in mechanical enterprise license pool): a CFD analysis of the clapper shut off due to emergency condition was carried out in order to calculate the clapper impact velocity. At CFD simulation end, the swing is still open with a minimum gap. The clapper velocity in this position and the fluid dynamic torque (end condition of CFD analysis) are the initial condition of the dynamic structural impact finite element analyses. Normally the dynamic structural impact FE analyses were performed using Ls Dyna which is not in the Ansys mechanical license pool. The goal is to perform the analysis by Ansys explicit solver thus being in the Ansys mechanical enterprise license till 2018 for free.
Curriculum
WORK EXPERIENCES
January 2012 – Present: FEA & Calculation Engineer at PetrolValves S.p.A.; Design calculation and verification with numerical simulations (Finite Element Analysis and Computational Fluid Dynamics), Valves, Oil & Gas.
Main activities: - FEA and CFD, also of advanced level, for product performance verifications and improvement
(R&D); - Developing hand calculation and technical report; - Workshop performance test supervision and data collection; - Numerical model validation through experimental data
April 2011 – August 2011: Internship at Tecnomare S.p.a. – eni Group. Design and verification activities in Chemical Process Engineering department
EDUCATION AND TRAINING
4 October 2011: Master degree in Energy Engineering – Hydrocarbon specialization at Politecnico di Milano, Faculty of Industrial Engineering.
Grade 106/110.
August 2010 – December 2010: Erasmus semester of study at the department of Petroleum Engineering and Applied Geophysics of
NTNU – Norwegian University of Science and Technology, Trondheim, Norway.
September 2009 – July 2010: First year of master degree in Energy Engineering – Hydrocarbon specialization at Politecnico di
Milano. Attendance of university courses and obtaining of a scholarship of eni corporate university.
23 September 2009: Bachelor degree in Energy Engineering at Politecnico di Milano, Faculty of Industrial Engineering.
Grade 101/110.
Fluids & Co | Vincent Soumoy
The right 1D - CFD choice for your digital transformation
It is sometime quite complicated to make a choice when a company is looking for a 1D piping tool. A lot are present on the market...they are all different, each of them has its own advantages. The author was involved with 3 of them (some since 1994), in Europe and North America, and also wrote a few papers. He worked with Flowmaster from 1994 to 2008 and from 2015 to 2017, with Flownex from 2017 to 2020 and with Hydrosystem since 2019. He will present below the three products and the best one for a few usages. After a brief history of the tools, you will see a description of the capabilities of each of them in the following area: User Interface, Ease of Use, Incompressible isothermal flows, Compressible and multiphase flows, Transient flows, Interface with CAD, CFD and FEA products, Main applications, Validation and Pricing.
This presentation is done considering our actual knowledge of the various tools and the original document was sent to representative of all products in the case where they would add any comments namely as far as recent of future capabilities would be concerned.
Each situation is different, the needs of your company are not necessarily the same as another society, they may also have changed with years. Do the right choice for your digital transformation.
Curriculum
Canadian Permanent Resident but Franco-Belgian nationality physicist, specialized in fluid mechanics, Diploma Course of the Von Kannan Institute in 1987, Vincent worked since more than 25 years in the simulation domain, namely in fluids (CFD).
Initially Research and Application Engineer in the industry, he wrote theoretical & empirical bibliographies, set up a multiphase flow software, validated results with experiments, and drew conclusions in an industrial pollutants study or in coating phenomena. He collaborated with international laboratories and participated in seminars and congresses.
He later moved Lo various software editors, as account manager, following SME and main accounts in Europe from cold calling and prospection, to standard and specific proposal elaboration.
He finally became Sales Manager of companies, the first one in Europe and the second in North America, set up the whole sales activity (markets sectors, new products, CRM…).
Covered end-to-end sales processes from analyzing client needs, creating tailored proposals, Lo managing sales/marketing/quality teams. He was also in charge of channel partner networks.
Vincent was to music and more particularly vocals interested, he sang and conducted various chords, with concerts in Europe and North America.
He created in 2015 Fluids & C°, based in Montreal, providing services and distributing software in various area, namely CFD but also Process and Data Management.
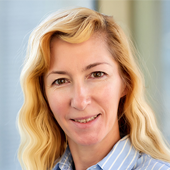
SIMUNE Atomistics | Anna Kimmel
Multi-physics approach for materials modelling
The increase in consumer demand pushes the industry to produce more advanced and cheaper products at a shorter time. Batteries must last longer, cars travel longer and emit less, consumer electronics must be lightweight, more powerful and desirably flexible.
To synchronise the demand with the production capabilities, the industry reorganises its manufacturing cycle by employing modern technologies for product creation and materials screening. The industry needs a robust tool for understanding how their products would work to achieve the production goal.
CAE built a strong reputation as a verification, troubleshooting and analysis tool. However, modern products become ever more complex and this leads to an increased need for multi-physics analysis.
Advanced atomistic modelling offers a way to explore the multi-physics of complex systems providing an insight into fundamental interactions at molecular and atomic level.
Here we present several case studies how modelling at quantum mechanical and/or atomistic levels makes possible to design novel materials and composites, predict their properties, understand multi-physics of processes happening in them.
Curriculum
Dr A. Kimmel, Business Development at SIMIUNE Atomistics, has over a decade of experience in development, application and distribution of computational software for materials modelling. She obtained her PhD degree in Theoretical Physics in 2005, and her career path includes both, academical and industrial experience. She has been working for various academic institutions including University College London, UK, University of Nevada, US, CIC nanoGUNE, Spain as well as for industry sector such as National Physical Laboratory and OXIREC, UK. Dr Kimmel is an expert in multiscale techniques, interfacial phenomena and AI applied for materials modelling. As a Business Development, she is responsible for the SIMUNE products range in European and Asian markets.