Friday 4 December 2020
Time slots: 10:00 AM CET | 6:00 PM CET | 2:00 AM+1 CET
Duration: 03:00:00
Automotive & Transportation Session | Part 3
AGENDA
Keynote Speaker: Danisi Engineering and Addfor | Marco Fainello
The role of simulation to boost driving assistance and autonomous driving development systems
Ducati Motor Holding - Ducati Corse Division | Gaspare Argento
Estimation of cycle average convective heat transfer coefficient on the underside of a racing piston for different layouts of oil jets
Chalmers University of Technology | Luca Boscaglia
Reduced-Order Thermal Modeling of Traction Motors
Taesung S&E | Kim Wootaek
Simulation of lubrication and splashing of an oil in reduction gear box using Moving Deforming Mesh
EnginSoft SpA | Paolo Bortolato
Fatigue Check of a Forged and Machined Component
RBF Morph srl | Marco Evangelos Biancolini
An advanced CFD post-processing tool enabled by adjoint and RBF mesh morphing allows the fast exploration of an arbitrary number of shape parameters effect on performances
CG CAE Sagl | Claudio Gianini
3D Elements in Composite Material Modeling for F1 cars
Aras Corp. | Matteo Nicolich
Why the Digital Thread is a Key Enabler of Systems Thinking at a major European Automotive OEM
Ansys | Eugen Meier
Photorealistic Simulation & Perceived Quality
Keynote Speaker
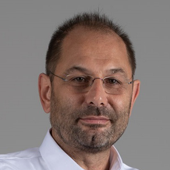
Danisi Engineering and Addfor | Marco Fainello
The role of simulation to boost driving assistance and autonomous driving development systems
The experience of recent years shows how the development of driving supports and autonomous driving needs simulation to be effective.
At the same time the requirements for simulation are evolving towards integration of different fields and their use is moving from being just specific expert tools to support bigger perspective decisions, at strategic level.
Let's try to see how this process is shaping the development of simulation tools and the process to use them.
Curriculum
Marco Fainello https://en.wikipedia.org/wiki/Marco_Fainello Mechanical Engineer, since 1990 he has been working in automotive industry, mainly high performance cars and motorsport racing, research and development and new technology applications.
With Ferrari he has been Performance and Simulation Director winning 8 F1 Constructor World Championships and 3 World GT Championships. In his last years in Ferrari he has been project manager of Ferrari FXX-K, 458 GTE LeMans 2014, 488 GTE/GTLM and 488Challenge.
During these thirty years he has also collaborated in different projects with Alfa romeo, Dallara Automobili, Porsche, Lamborghini and others.
He is now Chief Technical Officer at Danisi Engineering (automotive engineering and constructions) and Partner and Executive Director of Addfor (artificial intelligence applications).
He is advisor of different international companies in different industrial sectors, member of the Advisory Board of Mechanical Engineering at the Politecnico of Milan, technical reference of Smart Mobility Agency and member of scientific comitee of MASA (Modena automotive Smart Area).
For his professional achievements has been honored by Italian President with Cavaliere al Merito della Repubblica https://www.quirinale.it/onorificenze/insigniti/138680
Technical session
Ducati Motor Holding - Ducati Corse Division | Gaspare Argento
Estimation of cycle average convective heat transfer coefficient on the underside of a racing piston for different layouts of oil jets
Oil jets are widely used in high performance and racing engines in order to prevent the piston from overheating and protecting the engine from serious damage. The oil flowing across the underside of the piston helps cooling off the component, so the heat is transferred to the oil.
Typically, the oil is sprayed from a nozzle installed at the bottom of the cylinder. Depending on the number, diameter and location of the nozzle’s holes the resulting heat transfer performance will be different.
The main goal of this work was to find an alternative nozzle layout having a lower oil flow rate but with the same heat transfer performance. Three geometries, different from the reference one for number of holes, diameters and trajectories, have been studied. Their performance was assessed based on the cycle average convective heat transfer coefficient values on the underside of the piston.
All simulations were performed using the commercial mesh-free CFD software Particle Works.
Curriculum
After his Master’s Degree in Mechanical Engineering at the University of Bologna, Gaspare Argento worked for two years as CFD Engineer at Nais Engineering, a University of Bologna Spin-Off. In 2012 he joined the R&D Office at Ducati Racing, a Ducati Motor Holding’s department that focuses on the design and development of racing bikes for the MotoGP and SBK World Championships. Currently Gaspare leads the 3D CFD Engine activities.
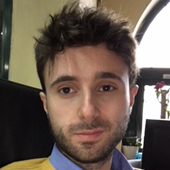
Chalmers University of Technology | Luca Boscaglia
Reduced-Order Thermal Modeling of Traction Motors
This study presents an approach based on Reduced-Order Modeling (ROM) using Machine Learning to predict the thermal behavior of an electric motor for a traction application.
Curriculum
Luca Boscaglia received his B.Sc. and M.Sc. in electrical engineering respectively from University of Napoli Federico II and Politecnico di Torino, in Italy. He worked and collaborated in several projects with ABB Traction Motors in Västerås, Sweden, and ABB Low Voltage Motors and Generators in Vittuone, Milan, working in R&D mostly in thermal design and fluid dynamic computations of electrical machines. Currently, he is pursuing his PhD studies at Chalmers University of Technology in Göteborg, Sweden, on Electrical Machine Design for Traction and Vehicle Applications.
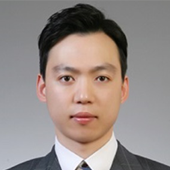
Taesung S&E | Kim Wootaek
Simulation of lubrication and splashing of an oil in reduction gear box using Moving Deforming Mesh
For the purpose of the sufficient lubrication and cooling of reduction gear system, it is important to establish optimum gear box design such as oil path holes and baffles to ensure lubrication and cooling performance. In order to predict them, CFD simulation was carried out using MDM(Moving Deforming Mesh) technique employed in Ansys Fluent for rotating gears and VOF(Volume of Fluid) for multiphase flow regime. In the present study, power distribution type reduction gear box which has been ordered recently for installation in high speed train of 260-320km/h grades was considered. As the results, transient nature of highly violent multiphase flow by gear churning was simulated successfully with proposed numerical schemes. We would like to explain analysis results in accordance with suggested simulation models in this presentation. Additionally, temperature prediction from convective heat transfer induced by oiling flow is going to be introduced for further investigation.
Curriculum
6 years experiences in CFD (mainly, Automotive and Transportation area)
3 years experiences in automotive paint shop design at plant company
Expertise in vehicle aerodynamics/fluids/thermal CFD
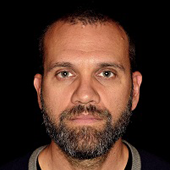
EnginSoft SpA | Paolo Bortolato
Fatigue Check of a Forged and Machined Component
As many designers had the opportunity to experience, it is not simple and, many times, not even appropriate to rely on FE analysis or hand calculations to evaluate the fatigue behavior of a mechanical component.
In the traditional approach the triaxiality of the stress tensor is not considered, the pre-stress field are omitted and notch effect, finish surface and chemical or heat treatments are usually not accounted for correctly, so it's very easy to make a mistake. The points where the maximum stress or the maximum stress amplitude occur, could not be the worst locations for fatigue behavior.
Therefore, it is necessary to use a dedicated software as FEMFAT 5.4 to exactly identify the points that could lead to the beginning of cracks and to accurately estimate the fatigue life of the component.
During the webinar, after a quick fly over the basic concepts of fatigue theory, I'll show the new approach followed to perform the fatigue analysis of a very important component for a Roller Coaster car, showing the benefits of FEMFAT use. The influence of the surface finish and how it contributes to the fatigue behavior of the component will also be highlighted.
Curriculum
Mechanical Engineer with over 20 years of experience mostly in technical areas and R&D. Good experience in virtual prototyping and theoretical analysis of structural problems.
Deep knowledge of multiple commercial CAE and CAD tools.
Manager of consultancy services.
RBF Morph srl | Marco Evangelos Biancolini
An advanced CFD post-processing tool enabled by adjoint and RBF mesh morphing allows the fast exploration of an arbitrary number of shape parameters effect on performances
Over the last decades the maturity of the CFD solvers and their companion adjoint solvers made possible the computation of the sensitivity of an observed performance (a pressure drop, a drag coefficient, a downforce) with respect to the shape of the part. It is nowadays a very well consolidated practice to explore shape sensitivity maps helping the designer to decide where moving outward/inward surfaces to improve the performance.
In the present study, we show how advanced mesh morphing allows creating, even at post processing stage, a variety of shape variations which intensities can be superimposed and the effect on performances previewed in real time. A very powerful design bench is obtained which allows to inspect the new shape and to evaluate, with a first order accuracy, the resulting performance value.
The tool is demonstrated for motorsport applications implementing Ansys Fluent for CFD and adjoint solution and its advanced mesh morphing module, RBF Morph, for the definition and control of shape parameters.
Curriculum
Marco Evangelos Biancolini, phd in Mechanical System Design, is an Associate Professor of Machine Design at the University of Rome “Tor Vergata” since 2000. He is the author and the owner of the RBF Morph technology, a partner of ANSYS since 2009, an Honorary Member of Technet Alliance since 2014. He is currently coordinating two European projects MeDiTATe and CAE Up. The main research interest is in CAE and in Radial Basis Functions for Engineering Applications.
CG CAE Sagl | Claudio Gianini
3D Elements in Composite Material Modeling for F1 cars
Composite materials are seeing a constantly increasing usage in every product and their industrial and large scale utilization presumes that also the production technologies are compatible with the costs, the time and the quality required in our days. Moreover, given that the structural analysis of components is today an integral part of the design process of any structural element, also the approach to simulation and the related software tools have to be raised at the necessary level in order to perform accurate and reliable calculations. In this job we will illustrate how the classical approach used to model parts made out of FRP (Fiber Reinforced Plastics) – i.e. using shell elements - has given wrong results and has led to the failure of the wishbone of a Formula 1 car, and how it was possible to identify the source of the error (and to correct the design) by switching to a higher modeling level, using 3D elements with orthotropic material properties to properly catch the phenomenon that was hidden behind the traditional simulation technique.
Curriculum
Claudio Gianini is a Mechanical Engineer with almost 30 years of professional experience in numerical simulation of the thermo-structural behaviour of complex mechanical assemblies. He has more than 15 years experience in Motorsport (Ferrari F1, Toyota F1, Sauber F1, Porsche LMP1).
He is the Author of two manuals dealing with the Computer Aided Structural Design and more than 25 articles concerning the usage of the Finite Element Method in the industrial practice.
He is the founder of the Swiss based consultancy Company CG CAE Sagl.
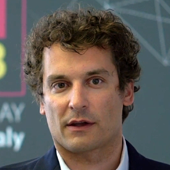
Aras Corp. | Matteo Nicolich
Why the Digital Thread is a Key Enabler of Systems Thinking at a major European Automotive OEM
The increasing complexity of product development scenarios, such as Connected, Autonomous, Shared and Electrified (CASE) poses new challenges: the requirements of the systems and their interactions grow to a size which is challenging to manage with traditional approaches. New mobility business models require thinking about a vehicle not just as a product, but rather as a system within a complex system-of-systems.
Model Based Development provides the framework to develop the vehicle using holistic systems thinking and simulation for continuous exploration and validation. However domain and subsystem silos challenge the adoption of Systems Thinking and reuse of knowledge across the enterprise.
The presenters propose approaches and platform characteristics to facilitate the flow of information across domains, and between system designers and simulation engineers, through the realization of a custom, domain-independent, system-centric digital thread.
Such a digital thread enables, the reuse of previous data and knowledge and provides a highly-customizable data management infrastructure for structured data accumulation that forms the basis of Machine Learning and AI applications to further accelerate the vehicle development process.
Curriculum
Matteo Nicolich is product manager with mechanical engineering and aeronautics backgrounds and deep experience in optimization, analytic decision making, and CAE process automation. He actively collaborates with multiple working groups as part of NAFEMS, INCOSE and ProSTEP iViP associations to create the connections between simulation and product design process and foster the adoption of System Thinking and simulation-driven design practices.
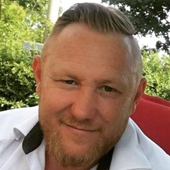
Ansys | Eugen Meier
Photorealistic Simulation & Perceived Quality
Virtual validation processes are the key to shorten development time and reduce dramatically costs for prototypes. Ansys offers a portfolio of different tools that help to achieve great quality and meet quality and aesthetic regulations. Our measurement devices deliver accurate inputs for simulations and guarantee the reliability of the obtained results.
In my presentation I’m going to introduce a real material selection use case and speak about the possibilities of postprocessing light simulation results for day and night time conditions. Head Up Displays got very popular and are nowadays affordable also in mid class vehicles. The development is challenging, and potential defects are materialized by complex metrics to validate for optical system acceptance. It is not always easy to build a common understanding on how these metrics will influence the final user experience. ANSYS SPEOS provide a complete toolset to address these challenges. Finally, software testing can be performed on an isolated standard display or using rest bus simulation to feed HUD software inputs.
Texture mapping and physics based Human vision make our solutions unique and add the “imperfection” that you experience in images in your daily life.
Curriculum
As the Manager Application Engineering, EMEA my team and I have a focus on Lighting and Visualization topics working together with customers in all industries dealing with lighting topics. I started my career as an Application Engineer at Optis and continued as a R&D Lighting Engineer at SMR Automotive GmbH. I have over 7 years of experience as Lighting Engineer within the automotive area including design, development, optimization, simulation and testing of lighting devices according to legal requirements and customer needs.
Projects: Renault Scenic STI, Opel Insignia Puddle Lamp, BMW F39 Xcite STI and HC2, BMW G2x (3 Series) STI HC2, Porsche Cayenne E3 STI, Daimler MFA2 W177 STI and BSM and many other.
I supported engineering teams at several OEMs and conducted workshops and trainings using SPEOS Software in different CAD Environments.
I spend my free time doing arts (carving, drawing, painting), working in my garden, traveling and reading.