Thursday 3 December 2020
Time slots: 10:00 AM CET | 6:00 PM CET | 2:00 AM+1 CET
Duration: 03:00:00
Aerospace & Defense Session
AGENDA
Keynote Speaker: AIRBUS HELICOPTERS | Gerard Goninet
Logistic Chain improvement with digital
Italian Aerospace Research Center - CIRA scpa | Roberto Scigliano
Best Practice about Thermal Protection System Design of the Hexafly-INT Hypersonic Vehicle
Elettronica Group | Alessandro Calcaterra
Multi-domain simulation to foresee issues in defense industry
RINA | Emiliano Costa
Toward a computational coupled procedure for the probabilistic design of missile radomes flying at supersonic regimes
GE AVIO SRL | Donato Magarielli
CFD-based aeronautical turbomachinery case study in the EU-funded LEXIS project
Leonardo SPA | Giuseppe Agresta
FEM Multibody analysis for optical stability evaluation
CIRA - Italian Aerospace Research Center | Francesco Di Caprio Structural optimization of Separation Spring Support Assembly of VEGA-C interstage 2/3
Neural Concept | Pierre Baqué
Deep Learning for Engineering Applications: Industrial Benefits and Transformation of Processes - Aerospace Case Studies
Digital Product Simulation | Patrick Grimberg
COLLABORATIVE ENGINEERING - How to bridge silos to address complex product development
CYBERNET SYSTEMS CO.,LTD. | Koji Yamamoto
Designing Non-homogeneous material using Multiscale.Sim for Ansys Workbench
Keynote Speaker
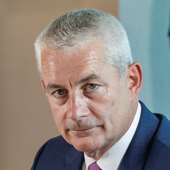
AIRBUS HELICOPTERS | Gerard Goninet
Logistic Chain improvement with digital
Within a worldwide network of plants & suppliers, Digital is a powerful tool to improve and optimize simultaneously all key performance indicators such as lead time, inventories, environnement (CO2), cost and quality.
Based on Airbus Helicopters new industrial model, logistics must be optimized to deliver the best value for our customers.
Digital brings us a lot of opportunities to define and assess our new model, simulate the way to operate a new logistic platform and will enable us to support the continuous improvement using digital twins.
Curriculum
Since 2019 to present, Head of Production flows
From 2017 to 2019, Head of tranformation project for mechanical product & services.
From 2015 to september 2017, Industrial Site Marignane Vice-President in Airbus Helicopters (managing Airframe, Dynamic Systems, Electrical Systems, Painting, Marignane Site, Cost Management Project). Airbus Helicopters is a subsidiary of Airbus Group.
From 2015 to june 2017, President of Team Henri Fabre association (Major project aiming to gather Public and Private around a common view as to create un new industrial model called the future extended company).
From 2010 to 2015 Industrial Site Marignane Vice-President at AIRBUS HELICOPTERS
Technical session
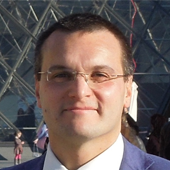
Italian Aerospace Research Center - CIRA scpa | Roberto Scigliano
Best Practice about Thermal Protection System Design of the Hexafly-INT Hypersonic Vehicle
Object of this presentation is to show how the ANSYS advance modelling capabilities let to effectively handle complex multidisciplinary design research projects like the Hexafly-INT. In particular, this project, funded by European Commission by means of the 7th Framework Programme, intends to test in free-flight conditions an innovative gliding hypersonic vehicle with several breakthrough technologies on-board. The vehicle design, manufacturing, assembly and verification is the main driver and challenge in this project. Prime objectives of this free-flying high-speed cruise vehicle shall aim at:
• a conceptual design demonstrating a high aerodynamic efficiency in combination with high internal volume;
• controlled level flight at a cruise Mach number of 7 to 8;
• an optimal use of advanced high-temperature materials and structures;
Present research describes the aero-thermal design process of the Experimental Flight Test Vehicle, namely EFTV and Experimental Service Module, namely ESM, leading to the definition of a proper Thermal Protection System (TPS).
Curriculum
R. Scigliano is a Ph.D. Research Engineer at the Italian Aerospace Research Centre (CIRA) in Capua (Italy). He obtained his Master Degree in Aerospace Engineering in 2005 at “Università degli studi di Napoli Federico II” in Naples (Italy). Scigliano won a Ph.D. Research scholarship funded by the European project Marie Curie RTN “MADUSE” in 2006. In the context of his Ph.D. he worked as research engineer at RENAULT sas in Guyancourt (France) at the research department for Vibro-Acustic group. He obtained a Ph.D. in Mechanical engineer at UTC (France) in 2009. At the end of 2009, Scigliano joined CIRA. The author is actually part of thermo-structures and thermal control technologies and design in structures and materials department. Scigliano is actually working at three main ESA / EU funded project, such as Hexafly-INT, Space Rider and Stratofly. Scigliano has 50 scientific publications in international conference, 8 paper published on the International scientific paper.
Elettronica Group | Alessandro Calcaterra
Multi-domain simulation to foresee issues in defense industry
Nowdays new emerging technologies can help designers to collect several information on several different elements of a project. Computer-aided engineering is a key element to merge different computing domains to get a greater physical insight. Simulation environments such as electromagnetic, thermal, mechanical needs to be taken into account at the same time to save costs and risks. This because they share the same simulation models, allowing iterative optimizations to be sure that changes in a specific domain does not affect others.
In this work we share a case-of-study about how a combined thermal-mechanical analysis of a radiating element has demonstrated to be useful to identify weak points, otherwise noticeable only during thermal stressing tests.
In details, the soldering between the antenna balun and the circuit was destroyed by the different thermal expansions of the materials. Although the electromagnetic model returned good results, more optimization was required on the mechanical model.
We reproduced the heat absorption of the structure and the consequent deformation: with a combined approach we developed a new shape of the balun, showing how the merge of different simulation environments leads to an antenna redesign to comply electromagnetic and thermal performances.
Curriculum
Alessandro Calcaterra was born in Rome, Italy, in 1993. He received a B.Sc. and M.Sc. (both summa cum laude and highest honours) in Electronic Engineering from “La Sapienza” University of Rome, Italy, in 2014 and 2017, respectively.
He attended two specialization courses reserved to the highest marks students and a specialization course from ESoA where he could deeply improve his knowledge in antenna design.
In his career, he worked as Microwave designer both for telecommunications and for electronic warfare systems.
Since 2019 he is working as Antenna Engineer in the Antennas&Microwaves Department at Elettronica S.p.A., where he is responsible of several items from the early design stages to the production.
At the same time, he is attending a PhD in Applied Electromagnetism at “La Sapienza”, University of Rome, where he is designing novel kind of antennas and developing innovative techniques to improve the electromagnetic propagation in lossy media.
His main research interests are UWB antennas, phased arrays, mathematical models for electromagnetic scattering and leaky-wave antennas.
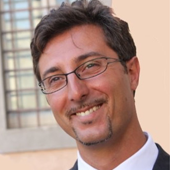
RINA | Emiliano Costa
Toward a computational coupled procedure for the probabilistic design of missile radomes flying at supersonic regimes
The requirements concerning the increase of speed performances of missiles yield to thermo-structural issues of several components including the radome. Being the missile’s nose, such a component influences not only the aerodynamics of the missile, but also the environmental protection of sensitive electronic equipment and microwave transparency. In this paper an automated procedure for the fast calculation of structural stresses in radomes flying in steady state supersonic conditions is described. Such a tool, implemented through the MAPDL software, incorporates the Modified Newtonian Method to analytically determine the aerodynamic loads over the external surface of the radome. The pressure distribution calculation was preliminarily verified using the experimental data of a wind tunnel test. The proposed tool paves the way to the development of a computational coupled procedure for the probabilistic design of ceramic radomes undergoing supersonic loading.
Curriculum
Emiliano Costa is a Principal Engineer in the Industrial Design & CAE team at RINA. He has a Ph.D. in Energy and Environmental Engineering and over 15-years of industrial experience in the CAE sector. He specializes in computational fluid dynamics and computational structural modelling and analysis. He used to be the coordinator of the RBF4AERO project and the Principal Investigator of the Experiment n. 906 of the FORTISSIMO project.
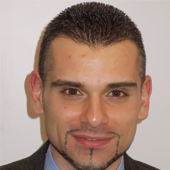
GE AVIO SRL | Donato Magarielli
CFD-based aeronautical turbomachinery case study in the EU-funded LEXIS project
The EU-funded LEXIS project (Large-scale EXecution for Industry & Society, Grant Agreement ID: 825532) aims to build an advanced, geographically distributed, HPC infrastructure for Big Data analytics within three targeted pilot test beds: Aeronautics, Weather and Climate, Earthquake and Tsunami. Within the first one led by Avio Aero, the industrial applicability of last generation HPC/Cloud/BD platforms supporting the execution of sophisticated CAE tools to examine the complex flows behavior in aeronautical engine components is under investigation.
From both a digital technology and business perspective, Avio Aero intends to obtain a marked step change: less time-consuming CAE analyses that exploit newly designed, improved or tightly coupled HW/SW components opening the doors to the “real time” design approach.
Aimed at drastically reducing the execution time of fluid dynamics analyses on low pressure turbines, the turbomachinery case study presented here deals with the improvement of the CFD solver TRAF. The development of a newly designed GPU-enabled version of this code is currently underway with promising results in terms of speed up compared with the consolidated one running on solely CPU-based HPC systems.
Curriculum
Electronic engineer with ~13 years’ experience, covering successful technical roles in different professional gyms: Software Designer in Public & Industrial Research, Signaling Engineer in Railways and currently Digital Technology Product Manager in Aviation.
Skilled to leverage the benefits of Digital Technology to address Engineering and Test Center needs & strategies while managing costs & risks, I’ve been working for 6 years at Avio Aero, a General Electric Aviation business.
Comfortable with facing new business challenges in complex environments implementing cutting edge digital solutions, my professional interests are in the areas of Computer-Aided Engineering, Computer-Aided Testing, Product Lifecycle Management, High Performance Computing, Big data management, and Artificial Intelligence.
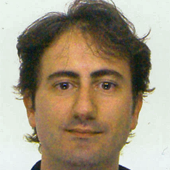
Leonardo SPA | Giuseppe Agresta
FEM Multibody analysis for optical stability evaluation
Today products and systems are more and more integrated with many disciplines. This is the domain of the Multiphysics where people and competencies are mixed together to optimize the whole system, achieving very different performances at the same time.
Big OEMs are seeking this approach even with the help of simulation software that allow to dive into this complex phenomena, one real example is the Leonardo Electronics Division (LED) multi-sensor, gyro-stabilized turret system designed for airborne surveillance applications.
Here kineto-dynamics analysis with deformable structures are coupled together with control system at the same time to guarantee high accuracy on a high-fidelity virtual model.
Curriculum
Mechanical engineer with more than ten years of experience in the design and analysis of mechanical systems.
Currently I’m the leading designer for the Leonardo MTG “Lightning Imager" thermo-mechanical project and the "Environmental Verification Specialist" for the Leonardo Electronic division.
After graduation, I co-operated with the University of Pisa in drafting the Safety Analysis Report for PHWR Atucha II NPP and for five years I worked in ALTRAN SPA in the role of external consultant for LEONARDO - FINMECCANICA.
During this period I specialize in the design of both composite and metal structures working on the Mechanical design verification for the Leonardo “PRISMA” project and participating in the development of the Leonardo- METOP SG “3MI” design.
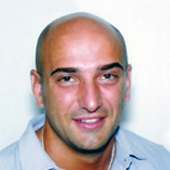
CIRA - Italian Aerospace Research Center | Francesco Di Caprio
Structural optimization of Separation Spring Support Assembly of VEGA-C interstage 2/3
The possibility of obtaining highly efficient structures is always a fundamental goal to which all designers aim, and when they deal with high-tech structures, like those ones for space applications, this goal become mandatory.
The reduction of structural mass for components of space crafts is a strategic aspect, since it can be transposed to competitiveness improvement of the entire products. Indeed, the lower structural weight leads to an increase in performance which often leads to an increase in payload capacity or a reduction in operative costs. Considering space launchers, these kinds of advantages are more remarkable when the optimized components are installed in the last stages (multi-stage launchers).
The presented work shows the design methodologies that led to the manufacturing of the separation spring assembly of the Interstage 2/3 of the VEGA-C launcher.
The separation system of the Interstage 2/3 of VEGA-C, developed in the framework of an ESA project (AVIO spa was the prime and CIRA was subcontractor) plays a primary role, being responsible for ensuring the correct execution of the separation between the second stage (Z40) and the third stage (Z9). The design of these components was carried out with a custom optimization procedure which use the commercial software FEM Ansys and modeFRONTIER. The final products are characterized by a very high specific load capability (applied load to component mass ratio) in compliance with the changeling functional requirements.
Curriculum
Francesco di Caprio, is an aerospace engineer with a specialization in structure analysis. He achieved the PhD in Aerospace Sciences and Technologies, with a thesis on the development of fast numerical procedures to be used in preliminary stages of damage tolerant composite structures design.
He has been working with CIRA (Italian Aerospace research centre) since 2011, and in particular he works in in the Airframe Design and Dynamic Laboratory, under Structure and Material Division.
Neural Concept | Pierre Baqué
Deep Learning for Engineering Applications: Industrial Benefits and Transformation of Processes - Aerospace Case Studies
We will show how Geometric Convolutional Neural Networks (GCNN), a Deep-Learning approach, can empower design engineers with surrogate models of CAE solvers such as CFD and FEA. The novelty of the approach lies in the usage of physical instead of parametric space as a reference for the Deep Learning process of Neural Networks. This makes it possible to exploit raw, non parametric CAD / CAE source data for training the surrogate models. As the first application example, we will report the performances of GCNNs on the problem of thermal simulations for satellite panels. The placement of electronic components and the efficient design of the cooling system are essential to reach the desired performances while ensuring a good longevity of the satellite. After reviewing the Deep Learning aspects on how the Neural Networks were trained with CAE and CAD data, we validate, on a dataset of hundreds of simulations, the Deep Learning thermal predictions with the CAE tool used as the Ground Truth. We discuss the impact on the design workflow, by integration within a CAD platform to deliver quasi real time results. Other examples of quasi real time CAE surrogates for CFD (aerospace external aerodynamics with capturing of shock waves) and for radiofrequency simulation (antennas for satellite telecommunications) will be reviewed, covering the aspect of validation with the CAE Ground Truth, uncertainty estimation and the practical relevance of surrogate models in the design process.
Curriculum
Pierre Baqué received an engineering degree in Applied Mathematics and a Masters degree in Operations Research from Ecole Polytechnique. After working as an Engineer for Credit-Suisse in London, he joined the Computer Vision Laboratory at EPFL. He got his doctoral degree in early 2018 under the supervision of Prof. Pascual Fua and Francois Fleuret. His research focused on Deep Structured Learning and Variational Inference applied to Computer Vision. As a result of his doctoral thesis, Pierre took the leap as an entrepreneur and founded Neural Concept in 2018.
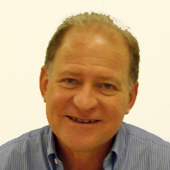
Digital Product Simulation | Patrick Grimberg
COLLABORATIVE ENGINEERING - How to bridge silos to address complex product development
Collaboration means not only bridging the traditional silos - multiple disciplines, heterogeneous systems, different and incompatible tools, various process with their own goals, always more complex and global organization of the work - but to re-create a connection between all the stakeholders while dealing with conflicting constraints and converge on an optimum design.
Big savings are required in the aviation industry, therefore implying technological changes such as moving towards more electrical devices within flight control systems. With significant weight reduction and flight efficiency improvements, aerospace companies will experiment tremendous cuts in fuel consumption.
In collaboration with a worldwide leader in aerospace manufacturing, DPS has been working on the redesign of an electromechanical actuator for aileron motion control. A high-level of performances had to be reached for the dynamics of the moving-parts without decreasing or jeopardizing the ability of the actuator to be easily integrated in the aircraft (e.g. proper space allocation, compatibility with power supply), to meet quality requirements (e.g. highest lifetime) and to deliver higher value (e.g. decreased manufacturing and operating costs).
Meeting these requirements lead to the implementation of concrete solutions enabling to work global, to identify and manage interactions, to promote concurrent engineering, to explore alternatives and to support effective collaboration as well as educated decision making and creation of system value.
KARREN was developed by DPS to provide a common and transversal space for designing complex products. KARREN offers cross-functional teams a customizable framework to align goals, to share roles and responsibilities, to benchmark progress at any time, to find optimal trade-offs, to respond to changes and take informed decisions for an optimum product.
This paper will demonstrate how KARREN was used to manage the development of an electromechanical actuator involving a cross-functional team and how it helped to leverage data-driven and model-based approaches to deliver an optimized and cost driven product.
Curriculum
Founder and CEO of Digital Product Simulation, a consulting company based in Paris recognized for its know-how in modeling, integration of digital simulation within the process of industrial products design and design optimisation.
Graduated in engineering from ESTP and a Master of Science in Structural Analysis from UCI, Patrick joined a start-up in Los Angeles in 1981. Hired in 1989 by DASSAULT SYSTEMES, he managed a technical team supporting customers in AEC and Shipbuilding. Patrick created DPS in 1997, following 2 years as sales manager of a consulting firm.

CYBERNET SYSTEMS CO.,LTD. | Koji Yamamoto
Designing Non-homogeneous material using Multiscale.Sim for Ansys Workbench
Featuring high usability by providing nonlinear functions, Multiscale.Sim is a fully compatible add-in tool, embedded in the Ansys Workbench environment. Helping you design composite materials such as fiber or filler, reinforced plastic, porous, lattice and honeycomb, Multiscale.Sim enables you to understand macroscopic material behavior and material constants based on virtual testing of microstructure models.
In this presentation, high performance productivity of material design process is introduced, based on new analysis examples in which Multiscale.Sim and ANSYS Workbench products are linked. We expect to be able to provide the following findings from this presentation.
- Discover how to use the multiscale analysis technique to surmount complicated materials problems.
- Understand how to assess every material constant without costly experimental campaigns.
- Learn how to use Multiscale.Sim to overcome materials modeling and characterization challenges.
Curriculum
Work Experience
2005 - 2008 : Technical support engineer of ANSYS software.
2009 - 2018 : Development engineer of Multiscale.Sim
2018 - present : Development manager of Multiscale.Sim
Education
Master of Engineering, Tokyo University : Tokyo, Japan 2005.
Doctor of Engineering, Tohoku University : Sendai, Japan 2020.