Monday 30 November 2020
Time slots: 10:00 AM CET | 6:00 PM CET | 2:00 AM+1 CET
Duration: 03:20:00
Automotive & Transportation Session | Part 1
AGENDA
Keynote Speaker: Shift2Rail Joint Undertaking | Carlo Borghini
Shift2Rail: Moving European Railway Forward
Ricardo | Martin Brada
Thermal Simulation of an Oil-Cooled E-Motor
Pierburg Pump Technology Italy Spa | Giorgio Peroni
Electrically-Actuated High-Speed Pumps: Layout Definition and Integrated Procedure to Design Optimization
BETA CAE Systems SA | Nikos Tzolas
Performing DOE Studies in Occupant Protection using BETA CAE tools
Ducati Corse | Stefano Rendina
Ducati Digital Process Innovation
HPE COXA | Francesco Porta
Particleworks MPS method validation for oil piston cooling jets in a high-performance engine application
Ansys Inc. | Sandeep Medikonda
Mesh morphing techniques for the numerical analysis of flexible PCBs
Endurica LLC | William Mars
Breaking the computational barrier to simulating full road load signals in fatigue of elastomers
FCA | Giancarlo Gotta
BEV performances by freeware softwares: faster, cheaper. And better too?
Dassault Systemes | Danilo Di Febo
EMC Simulation of an Electrical Vehicle Powertrain
Keynote Speaker
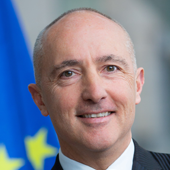
Shift2Rail Joint Undertaking | Carlo Borghini
Shift2Rail: Moving European Railway Forward
Shift2Rail is the first European rail initiative to seek focused research and innovation (R&I) and market-driven solutions by accelerating the integration of new and advanced technologies into innovative rail product solutions.
The proposed initiative helps to boost the rail supply industry’s competitive edge, introducing new market perspectives and offering significant employment and export opportunities.
In order to achieve these ambitious targets, the R&I Programme builds on digitalization, automation, virtualization and scientific advances to enable the transformation of the rail system. In the current programming period, the Programme has the ambition of delivering technological solutions that will result in increased capacity of existing networks, reducing the lifecycle cost of the different systems and increase the overall punctuality of services. Virtualization and engineering simulation are key elements of the Programme and should contribute to accelerate the market uptake of the innovative solutions.
Curriculum
Carlo Borghini - Executive Director, Shift2Rail Joint Undertaking
Mr Carlo Borghini is responsible for the overall management of the Shift2Rail Joint Undertaking activities since he took up the position of Executive Director in February 2016.
Prior to this posting, Mr Borghini held senior management positions in different domains in private and international organisations, at corporate level. He was the Deputy Executive Director for the SESAR Joint Undertaking (SJU) in Brussels from 2008 to 2014, and prior to this was Director and Chief Financial Officer (CFO) for the International Fund for Agricultural Development (IFAD), a specialised Agency of the United Nations based in Rome.
Mr Borghini holds a Master’s Degree equivalent in Business Economics and speaks Italian, French and English. He is married with three children.
Technical session
Ricardo | Martin Brada
Thermal Simulation of an Oil-Cooled E-Motor
Temperature prediction of windings is of importance during development of an oil-cooled electric motor. A new method using a particle-based CFD software solution has been tested and validated against experimental data with the aim to simulate violent multi-phase flow more efficiently than with traditional CFD codes based on finite volume method. The fluid simulation was used to acquire a heat transfer coefficient (HTC) map whereas an advanced technique of simulating air and oil flow field separately with different particle sizes was utilised at this stage. The HTC map was subsequently applied to a steady state finite element thermal model in order to solve for temperature field. The correlation with the experimental data was deemed satisfactory within the targeted tolerance.
Curriculum
I currently work as a thermal systems engineer in Ricardo China. In this position, I deal with a wide variety of technical problems related to heat transfer and fluid mechanics in both xEV and ICE cars.
I graduated with a major in applied mechanics from the Czech Technical University in Prague, Faculty of Mechanical Engineering. Before my current position at Ricardo, I worked as a CFD engineer in the field of external car aerodynamics for two years.

Pierburg Pump Technology Italy Spa | Giorgio Peroni
Electrically-Actuated High-Speed Pumps: Layout Definition and Integrated Procedure to Design Optimization
Electrically-actuated pumps for automotive applications belong to the Pierburg Pump Technology product portfolio since more than two decades. They consist typically of a hydraulic system, featuring dynamic or volumetric concept, driven by a dedicated electric motor and controlled by an electronics module. They found their field of application within the traditional ICE vehicles as well as within the alternative propulsion vehicles: with water systems (cooling), oil systems (lubricating, cooling) or air systems (braking assistance).
More recently, among the electro-actuated pumps the family of high-speed pumps has become more interesting for PPT since new applications have raised to be attractive for the automotive market. We refer specifically to the Active Purge Pump for Evaporative Emission Control System (EVAP) application and the Hydrogen Recirculation Blower for FCEV application.
As high-speed electro-actuated pumps we usually indicate devices having rotational speed above 20.000 rpm. Their working fluid is typically a gas, air or gaseous mixture. Their global layout is quite similar each other, consisting of a shaft fitting the dynamic impeller and the magnetic rotor and supported by roller bearings. Anyway, they may have dimensions and power absorption quite different, of course within the limits typically imposed to the automotive applications.
From the engineering process point of view, high-speed pumps require a fully dedicated procedure, able to take into account of targets of different nature at the same time. On one side, high rotational speed (20.000 - 60.000 rpm) is necessary in order to fulfill the pneumatic performance. On the other side, such high speed may be challenging for the life of the bearings due to the loads generated by the dynamic response of the rotating system.
To support the pre-design phase of the new generation high-speed pumps the simulation approach has been widely employed. Specific tools have been introduced in order to sketch the pneumatic subsystem and to evaluate the dynamic loads acting on the bearings and consequently their life.
Finally, all of these tools have been collected in one only workflow with the help of the modeFRONTIER ambient: the aim was both to integrate them in one only place and to link them through an optimization algorithm, obtaining a flexible tool able to deal with so different kind of applications.
The optimization procedure helps the engineer first to choose the optimum among all the possible layouts, exploring different relative positions of the impeller, the bearings and the magnetic rotor. Then, it helps to analyze a large number of variants, considering design constraints and limitations. Finally, it helps to detail and to keep under control possible trade-off between the pneumatic performance and the lifetime durability performance.
Curriculum
Giorgio Peroni (the speaker) holds the position of Modeling and Simulation Engineer at Pierburg Pump Technology Italy. He has obtained the Master’s Degree in Mechanical Engineering at the University of Pisa; after a period spent as a researcher at University, he joined the Company in 2009.
Its job is to conduct research activity on the field of fluid dynamics with specific applications to all the products of the Company, namely pumps and fluid dynamic systems for the automotive market. His expertise ranges from the field of volumetric and dynamic pumps to the valves, from the thermal-fluid-dynamic integration for electric products to the optimization applications.
BETA CAE Systems SA | Nikos Tzolas
Performing DOE Studies in Occupant Protection using BETA CAE tools
Occupant safety is among the most important studies during a vehicle’s design process. To achieve the highest possible standards of occupant safety, engineers simulate a wide range of crash scenarios. In each scenario different factors affect the occupant injury results and the most effective way to identify these factors is to perform design of experiments (DOE) studies.
DOE studies can be used to optimize the vehicle's structure and the restraint systems. For the latter case many different properties of the seat-belt, the airbag, the seat and of the coupling between them and the occupant can be used as design variables to examine the occupant injury results.
In this paper a DOE studies how occupant injuries are affected from different seatbelt parameters. A THOR-50M ATD is used in a front impact sled test. The sled test was setup in ANSA, BETA CAE Systems’ pre- processor, the Optimization Tool of ANSA set up the DOE and LS-DYNA was used to calculate the results. META, BETA CAE Systems’ post- processor was used to extract automatically and evaluate all responses (injury peak values and time history curves).
Curriculum
Nikos Tzolas - Studied at Technological Educational Institution of Thessaly from 2000 to 2005
Working at BETA CAE Systems S.A. from 2008 until now
Current Position / Tasks / Greatest Accomplishments
Works at Customers Service department of BETA CAE Systems, specialized in post processing applications. Develops tools inside META, the post processor of BETA CAE Systems, that automatically post process Crash and Safety results.
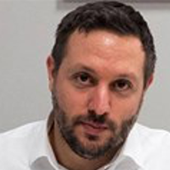
Ducati Corse | Stefano Rendina
Ducati Digital Process Innovation
Stefano Rendina, IT Manager, Ducati Racing, discusses how digital innovation is transforming the way we design, manufacture and service our products. Advanced simulations, data analytics, optimization are paving the road for a greener, safer and faster future. To maintain a technological advantage, a comprehensive approach to digital innovation has been put in place at Ducati.
Curriculum
Stefano Rendina, born in 1984, has been working for Ducati for 8 years.
He started as a systems engineer and help desk technician for the racing department, and then grew to become the IT Manager of Ducati Corse, a role he has held for 4 years.
His job consists in finding, and implementing, the most suitable IT solutions for the Ducati racing teams competing in the major international motorcycle championships, including MotoGP and World SuperBike, as well as managing all the related issues.
HPE COXA | Francesco Porta
Particleworks MPS method validation for oil piston cooling jets in a high-performance engine application
The present study involves the validation of the MPS meshless methodology for the simulation of oil piston cooling jets in a high performance engine application. A comparison between the approach using PARTICLEWORKS software implementing the MPS meshless method and the results obtained using STAR CCM+ software that implements the traditional finite volume calculation method with VOF multiphase model and Overset mesh will be presented. The MPS methodology makes it possible to quickly evaluate several different piston cooling configurations and geometries in early stage of engine design process.
Curriculum
Francesco Porta [20 June 1988, Reggio Emilia, Italy]
Professional Experience
- January 2020 - Present, CAE – CFD Team Leader at HPE-COXA srl
- August 2013 - January 2020, CFD Simulation Engineer at HPE-COXA srl
Education
- 2007-2010, Bachelor’s Degree in Mechanical Engineering, Università degli Studi di Modena e Reggio Emilia, Facoltà di Ingegneria di Modena
Internship at the Department of Engineering of Modena in collaboration with the Energy Efficiency Laboratory.
- 2010-2013, Master Degree in Vehicle Engineering, Università degli Studi di Modena e Reggio Emilia, Facoltà di Ingegneria di Modena
Internship at HPE-COXA srl as CFD Analyst.
Ansys Inc. | Sandeep Medikonda
Mesh morphing techniques for the numerical analysis of flexible PCBs
Flexible Printed Circuit Boards (PCBs) installed in complex shapes are increasingly being used in a wide variety of modern products ranging from smartwatches to automobiles. Their ability to survive high levels of shock and vibration along with the flexibility in connecting components and reduced package weights make them a desirable option. Given the complexity of PCB's, numerical modeling and analysis of such structures pose a major challenge and there is a need for clear, simple, and effective modelling techniques.
In this context, the Radial Basis Functions Mesh Morphing (RBF Morph) has been identified as a powerful mathematical tool to update the shape of a computational mesh by changing the nodal positions. In this work, a couple of different morph techniques have been developed and successfully applied to analyze flexible/curved PCBs. The methodology and the analysis results indicate that the morphing technology is arguably the simplest way to model flexible/curved PCBs.
Curriculum
Sandeep Medikonda currently works as a Senior Consulting Engineer at Ansys, Inc. and is responsible for providing efficient solutions to modern engineering problems using Ansys software products. He has a PhD in Mechanical Engineering from the University of Cincinnati and a master’s degree in Mechanical & Aerospace Engineering from the Illinois Institute of Technology (I.I.T), Chicago. As a graduate student, he was awarded the P&G Simulation Technology Scholarship in 2014 for his research contributions. In addition to being an active researcher, Sandeep also serves as an Associate Editor for the SAE International Journal of Materials & Manufacturing.
His research interests and areas of expertise include:
• Numerical modeling and structural analysis of Printed Circuit Boards (PCBs) and Flex-PCBs.
• Non-linear finite element analysis (involving impact, non-linear contact etc).
• Mesh-free methods (Discrete Element Methods & Element-Free Galerkin Methods).
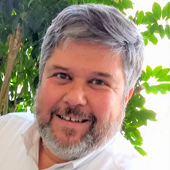
Endurica LLC | William Mars
Breaking the computational barrier to simulating full road load signals in fatigue of elastomers
Although modern computers are powerful and computing resources abundant, still, computing the impacts of full road load signals on durability of rubber parts has seemed to remain beyond the reach of even the largest industry players. The very large number of time steps involved, and the limited execution rate of typical finite element models has completely prevented the direct treatment of road load signals derived from track testing, from vehicle dynamical models or from a digital twin. In this work, we present the Endurica EIE nonlinear load mapping procedure, which provides a means by which the strain/stress histories resulting from full road load signals can now be rapidly generated. The procedure utilizes a series of pre-computed finite element solutions to populate a nonlinear map relating global load/displacement inputs to local strains/stresses within each finite element. For each time step of the full road load signal, the nonlinear map is used to obtain stress/strain results via interpolation. Examples are provided for 1-, 2- and 3-channel signal inputs, and applied to the following automotive components: a sway bar link, a control arm bushing, and a transmission mount. Input signals of several durations were studied as follows: 100, 1000, 10000 and 100000 time steps. The resulting analyses executed with as much as almost 4 orders of magnitude speed up relative to the alternative of a direct finite element solution, with error depending on map discretization (and therefore controllable up to an accuracy of about 10% in life). Importantly, the larger the number of time steps in the signal, the greater the relative analysis speed-up that is possible.
Curriculum
Dr. Will Mars founded Endurica LLC in 2008 to give product developers a simple and accurate workflow for analyzing the durability of elastomer products. 6 of the global top 12 rubber product companies are using Endurica solutions today. Dr. Mars remains active in rubber science with 60+ publications and patents in the area of elastomer durability. He is past editor of two scientific journals: Rubber Chemistry & Technology and Tire Science & Technology.
FCA | Giancarlo Gotta
BEV performances by freeware softwares: faster, cheaper. And better too?
Need to design, release and introduce a more affordable generation of battery electrical vehicles in the automotive market questions industry about efficiency of well established processes and traditional best practises. CAE discipline is no exception, most simulation environments and tools were developed to support internal combustion engine vehicle development and need some preliminary verification to be used for electric car applications too. This work assesses reliability of freeware softwares to estimate their performances, allowing thermal engineers priming their simulation models during early project develpment, saving time and improving risk management. Battery electrical vehicle heat generation and cooling capacity is sensitive to torque and speed profiles, then you have to explore many driving patterns to encompass all possible critical situations. Assuming freeware softwares provide fair enough simulation results, thermal CAE engineers can extract what they need by estimated vehicle performances, allowing performance expert concentrate their efforts to meet key customer requirements such as top speed, accelerations, driveability or range. A reliability assessment was performed estimating qualification lap times for electric cars attending official championships, relying on public available race results, regulations and vehicle specifications. All seasonal events were explored to introduce the largest possible variability due to different track layouts and environment conditions. Correlation between simulation and real results is encouraging, but in order to explore all selected freeware software features two additional investigations are planned for 2021,
Curriculum
Born in 1966 Giancarlo Gotta joined FCA in the 90s as CAE analyst, taking care of various chassis systems but collaborating with other department as well to develop new investigation methodologies. He has been acting as thermal systems performance engineer during the last fifteeen years, achieving the rank of Technical Fellow and promoting interfunctional collaborative efforts to drive vehicle development by simulation since the very beginning of a new project. As research paper author, he investigated 0d and 1d simulation sofware capabilities following the KISS design principle credited to Kelly Johnson and USNavy: whatever you do, Keep It Simple, Stupid.
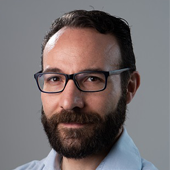
Dassault Systemes | Danilo Di Febo
EMC Simulation of an Electrical Vehicle Powertrain
This talk provides an overview of simulation solutions that address the challenges in the design of a three-phase inverter powertrain module , in particular, it addresses the EMC compliance, parasitic extraction aspects and impact of cables laid in to the vehicles. We start to evaluate the 3-phase system, limitation coming from the layout including the parasitic effect due to bond wire connection, this helps to reproduce the real scenario close to the prototype. The inverter will be integrate into the engine bay and connected to the electrical motor to estimate the emission. The engine bay will be integrate into full vehicles to evaluate the emission including the surrounding space.
Curriculum
Master degree Electronic Engineer at University of L’Aquila, 2012 PHD SCHOLARSHIP at the same University, Post Doc developing a numerical tool in Java object oriented for 2D data comparison using the FSV (feature Selective Validation.
Few years as a consultant in Altran Italy based in Mila as a RF Engineer for home appliance devices.
Join in CST Italy on 2017, as Sales and Application Engineer focused on DC/DC Converter, PCB application, Signal Integrity and Power Integrity, Electrical motor and power transformer Experience in a consultant company.
Now in Dassault Systemes, as a Solution Consultant Specialist in EUR-OMED Area, focused on DC/DC Converter, PCB application, Signal Integrity and Power Integrity, Electrical motor and power transformer.