Monday 30 November 2020
Time slots: 2:00 PM CET | 10:00 PM CET | 6:00 AM+1 CET
Duration: 01:30:00
The RecurDyn Experience 2020
RecurDyn software provides high-end features for the simulation of multi-body systems in dynamic conditions. Watch this online event to see the capabilities of the current version of RecurDyn and visit RecurDyn's virtual booth to chat with an expert. RecurDyn, connect to everything.
Multi Body Dynamics (MBD) is acknowledged as a branch of computational applied mechanics. The method was first formulated in the early Seventies in the USA and subsequently evolved into the numerous commercial products available today. While other simulation disciplines, such as Finite Element Method (FEM) and Computational Fluid Dynamics (CFD), are widely used in most industries, MBD still plays a marginal role and is definitely underexploited. Using MBD in an early stage of the design process leads to great and measurable advantages. MBD checks the capability of a moving system to perform the task for which it has been designed and, additionally, returns the sizing loads and other crucial information to properly perform downstream simulations.
RecurDyn is one of the most modern commercial tools for MBD simulation. It has been designed to cover both the classical needs of MBD and to overcome the limits of our competitors. More than 60 developers in Seoul (Republic of South Korea) are committed to developing the most powerful, flexible, open platform for the simulation of mechanical systems in dynamic conditions. The Graphical User Interface (GUI) is intuitive, so that new users can become productive in a short time. The solver, which has been improved over the years, exploits proprietary formulations that return high stability, low numerical damping, and allows for a wide spectrum of applications (from low to high frequency). The unparalleled power of RecurDyn is accessible via a programming interface (PNet) for the user to build specific toolkits to automate recurrent tasks, and even customized interfaces.
Another valuable advantage for customers choosing RecurDyn is the great support service available, which is delivered by FunctionBay's headquarters and its subsidiaries worldwide. FunctionBay’s technical network extends through Korea, Japan, China, Europe, the USA, and India. Our resellers’ distinguishing characteristics are their technical competence. FunctionBay's network executes thousands of hours of MBD simulation a year, worldwide, and this is the greatest value we can offer to our customers. No matter what you are trying to simulate: if MBD is applicable, we can do it with RecurDyn.
Some of the unique features included with RecurDyn are:
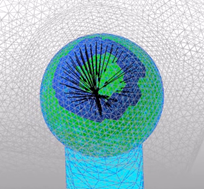
The most advanced contact technology on the MBD market
RecurDyn includes a wide library of analytical and mesh-based contacts that cover any type of application. The accuracy of the contacts is increased by specific surface mesh controls and the proprietary 3D smoothing technology.
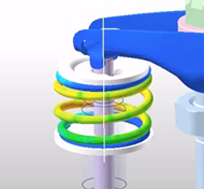
The premium Full Flex technology
While some of our competitors struggle to co-simulate MBD and FEM, RecurDyn handles non-linear flexibility with an efficient native approach. We call it Multi-Flexible-Body-Dynamics. Our equations of motion are rearranged to perfectly match the solver’s capabilities, returning unparalleled efficiency. The result is a real Transient Finite Element simulation in a real Multi-Body-Dynamics model.
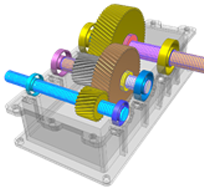
The drivetrain toolkit featuring KISSsoft technology
RecurDyn can predict the Total Transmission Error of gear-based systems in both steady and transient conditions. This type of calculation requires advanced virtual models. For mechanical components such as shafts, boxes, clutches, and couplings the standard RecurDyn features are used. For mating gears and bearings, RecurDyn embeds the KISSsoft technology, which delivers superior accuracy in contact analysis and stiffness prediction.
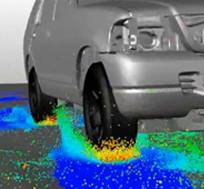
Co-Simulation with CFD: the ParticleworksTM interface
Pursuing the idea of integrating Multi-Body-Simulation with other simulation domains, RecurDyn offers an efficient interface that enables co-simulation with Particle-based computational fluid dynamics (ParticleworksTM from Prometech, Inc.). The interface is applicable to both rigid and flexible bodies, making RecurDyn capable of simulating a Fluid Structure Interaction (FSI) in dynamic conditions.
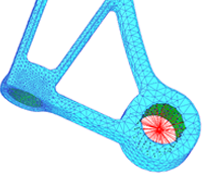
Proprietary Automesher
RecurDyn's strength in simulating flexible bodies would not be complete without an internal mesher. While external meshes can be used, RecurDyn's internal meshes are generated faster and preserve any features previously created on the body being discretized.
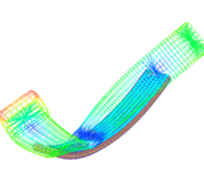
Reduced Flex Generator and Reduced Flex Technology
Of course, RecurDyn can use linear flexibility by importing the modal bases from external FE code. However, this would only make RecurDyn comparable to other tools on the market. RecurDyn is better because it features an internal FE solver, which allows for the preparation of linearly flexible bodies in accordance with the Craig-Bampton theory. This definitely eliminates the need for an external FE product.
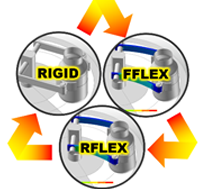
G-Modeling
The combination of automesher, full flex technology, reduced flex technology and reduced flex generator, makes the conversion of bodies from rigid to any of the available formulations child’s play. The G-Modeling assistant guides the user through all the phases and no information is ever lost. Final models can feature rigid, fully flexible and reduced flexible bodies simultaneously. If unsatisfactory, one can always change the formulation. This is what makes RecurDyn the market's most efficient tool for the simulation of flexible multibody systems.
AGENDA
Gear Lab, Italy | Davide Marano
NVH Analysis and Simulation of Automotive E-Axles
The sound made by electric vehicles’ axles is the result of the high-frequency whining noise generated by the electromagnetic forces of the motors, the gear meshing frequencies of the transmissions, the frequencies of the bearings and the high-frequency noise generated by the AC/DC converters. The Noise, Vibration and Harshness (NVH) characteristics of an electric axle are not comparable to the powertrain of a conventional vehicle. In fact, an internal combustion engine generally has lower orders with a higher sound pressure level (SPL), thus masking the higher orders from the transmission. An E-Axle, on the other hand, generally has higher orders with a lower SPL. Nonetheless, the high-frequency noise generated by the motor and the transmission is subjectively quite annoying. This paper discusses a methodology to analyze and simulate the NVH of an automotive E-Axle. The theoretical calculation of a Campbell diagram including the electrical and mechanical orders is presented and a constrained modal analysis of the system on mountings is performed to calculate its natural frequencies. The electric axle is modeled as a fully flexible multibody system and the forced response is calculated at the constant speed of the electric motor. The NVH output of the high contact ratio gears (HCR) is evaluated against the standard ISO-53 gear profile A. For this purpose, peak-to-peak transmission error (PPTE), gear meshing, and bearing forces are compared for both configurations. The influence of housing stiffness is investigated. The equivalent radiated power (ERP) of the housing in both the ISO-53 profile A and the HCR gear simulation is compared showing the reduction of the normal surface velocities. Critical areas for the design of the housing are illustrated with contour plots.
EnginSoft USA | Brant A Ross
High-Fidelity Simulation of Dynamic Axisymmetric Structures with Process Automation
Drivetrain components are required to withstand large numbers of cycles and various dynamic loading events. Accurate analysis of driveline components can be achieved by considering the dynamics in the system, as well as the structural characteristics of the components. An example is the simulation of the flexible boot of a constant velocity (CV) joint assembly that is used in an off-highway application with extreme transmission angles. Multibody dynamics and nonlinear finite element analysis techniques are used to simulate the boot behavior. The simulation techniques include replicating the assembly process and dynamic operation. The validation of this simulation shows excellent correlation between the simulation and the test regarding the collapse of the two outer folds of the boot (which form dimples), the shape of the boot, and the contact between the folds, all when rotating with a large transmission angle. Process automation was used to increase the efficiency of such simulations.
Curriculum
Ph.D. degree in Mechanical Engineering from Brigham Young University
7.5 years as an engineer at John Deere and General Motors
9 years with Mechanical Dynamics (ADAMS multibody dynamics software)
3 years with FunctionBay
16 years with MotionPort (founder, owner, president)
Current position / tasks
6 months with EnginSoft USA, who acquired MotionPort in May. We provide RecurDyn multibody dynamics software, Particleworks CFD software and related services to organizations across the USA.
FunctionBay Japan | Masakazu Goto
Dynamic simulation of gear transmission systems using Multibody Dynamics
Today, the demand for noise vibration (NV) performance is increasing with the growth of the battery electric vehicle (BEV) and hybrid electric vehicle (HEV) markets. Gear systems are used for power transmission in vehicles. However, despite the use of static analysis in the transmission design development process, the dynamic behavior of transmission systems is rarely simulated. However, dynamic behavior analysis and simulation of transient response are more important than before because gear transmissions are used at higher rotational speeds due to higher accelerations caused by BEV and HEV electric motors compared to internal combustion engine (ICE) vehicles. Gear meshing is one of the main causes of vibration in gear transmission systems. The vibration caused by gear contact is transmitted to the chassis via the shaft/bearing/housing. In order to estimate the behavior of the transmission system with high accuracy, "shaft deformation", "bearing stiffness considering clearance", "housing case deformation", and "gear contact stiffness variation" should be included in the analysis. "Shaft deformation", "bearing stiffness including clearance", and "housing case deformation" can be accurately considered within multibody dynamics (MBD) software. However, MBD is a simulation tool based on rigid body mechanics. Therefore, it is difficult for conventional MBD to deal with tooth bending and local deformation in gear contact analysis. In addition, calculation takes a long time to obtain accurate results in gear contact. There is some MBD software with gear-specific functions. However, its computational accuracy is uncertain, and this fact may be one of the reasons why dynamic analysis using MBD is not yet widely used in transmission analysis. It is clear that gear contact simulation must be verified. In this study, we verify the gear contact calculation results by comparing them with the experimental results. In this presentation, we will introduce the MBD approach, which can include changes in the stiffness of gear contact, and a simulation case study of vibration transfer from the gear to the housing case in the transmission system, as a method for predicting the behavior of the dynamic gear, along with the verification results.
Changzhou Vocational Institute of Mechatronic Technology, China | Liu Yi
Using RecurDyn in the design and simulation of the Overrunning Alternator Pulley
In order to solve the front-end accessory drive system (FEAD) problem caused by engine speed fluctuations, an Overrunning Alternator Pulley (OAP) was developed and a comparative study of CAE analysis and tests was conducted. Based on the multi-body dynamics theory, a virtual prototype model of the one-way pulley block was established. The model can accurately reflect its operating characteristics. On this basis, the factors affecting the operating characteristics of the OAP were studied, and some useful guiding conclusions were drawn:
(1) When the friction coefficient μ = 0.10-0.15, the wedge time of the needle roller, mandrel and outer ring will change significantly. As the friction coefficient increases, the wedge time is substantially reduced;
(2) The maximum contact impact force occurs at the contact point between the needle roller and the mandrel. The maximum contact force is generally about 4 times the stable contact force at 6000rpm (equivalent to the stable speed of the engine);
(3) Under different friction coefficients, the average contact force between the needle roller and the mandrel and outer ring after OAP wedging does not differ much, but the impact force can be reduced by reducing the friction coefficient;
(4) Selecting the appropriate spring stiffness and spring preload directly affects the wedging characteristics of the OAP during operation.
FunctionBay, Inc., Republic of Korea | Minsung Song
A Verification Study Using Co-simulation of the Dynamics and Particle methods on the behavior of a tractor mid-mower
The object of research in this paper is a mid-mower positioned in a tractor lawn mower. Even with some common CAE software, it was not easy to understand how this component works when mowing the lawn.
Therefore, this paper introduces a new CAE approach for the dynamic analysis of lawnmowers using the multi-physics configuration of RecurDyn software and Altair EDEM which interacts between the multibody object and bulky particles.
The mowing parts were modelled in RecurDyn with a series of real motions and the grass was modelled with Altair EDEM using a bonding force.