Thursday 3 December 2020
Time slots: 2:00 PM CET | 10:00 PM CET | 6:00 AM+1 CET
Duration: 02:00:00
Energy, Oil & Gas Session | Part 2
AGENDA
Keynote Speaker: Revolution in Simulation | Malcolm Panthaki
The 2-Year Old RevolutionInSimulation.org Community – Are You Being Left Behind?
PSRE Co (NTP Truboprovod) | Leonid Korelstein
Centrifugal pump simulation during waterhammer analysis
ZECO S.r.l. | Riccardo Orso
CFD analysis and optimization of a Kaplan turbine Draft Tube
Bosch Thermotechnology | Fatih Tolga Özdemir
Experimental Verification of Drop Test Simulations of Combi Boiler
CADFEM CIS | Oleg Zolotarev
Digital twin technology in the mining industry: Digital twin of a grinding mill
SVS FEM s.r.o. | Petr Konas
A parameter less shape optimization process allows to extend fatigue life of structural parts subjected to thermal fatigue
Keynote Speaker
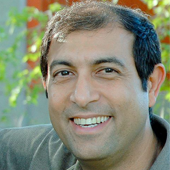
Revolution in Simulation | Malcolm Panthaki
The 2-Year Old RevolutionInSimulation.org Community – Are You Being Left Behind?
The democratization of simulation software is increasing the number of simulation users by one or more orders of magnitude. Similar dramatic expansions of use of complex technologies have been witnessed in other technology-driven industries. In each case, the expansion occurs when the nascent, complex, hard-to-use technology is packaged into a form that is simple-to-use, robust, affordable and accurate, and made available to everyone.
The free RevolutionInSimulation online community (Rev-Sim.org) was launched at the NAFEMS CAASE conference 2018. Rev-Sim provides professional resources and a collaborative community to help increase the impact and value of engineering simulation software (CAE) investments through the Democratization of Simulation. Here you’ll have access to success stories, news, articles, whitepapers, blogs, presentations, etc. to help you take your simulation investment to the next level. Experts have volunteered to be Topic Moderators, curating the resources and authoring blogs on various important next-generation simulation topics. You’ll also have one-stop access to simulation specialists and industry organizations, along with software and consulting service providers.
Curriculum
Malcolm Panthaki has over 30 years of experience developing simulation environments to enhance the effectiveness of the product development process, bringing simulation safely and robustly to the entire enterprise. At Abaqus Inc. (acquired by Dassault Systemes) Malcolm led the development of Abaqus/CAE. As an entrepreneur and founder of Comet Solutions and as the founder of the online community, Revolution In Simulation, he has helped reshape the dialog on bringing simulation to everyone that needs it, not just the experts. At Comet Solutions, he worked closely with key global customers such as NASA, Aerospace Corp., American Axle, GKN, Magna and ZPMC (China) to better leverage their simulation investments through intelligent simulation automation. As VP of Analysis Solutions at Aras, Malcolm leads the Aras strategy in the areas of MBSE and Simulation Management in Aras Innovator PLM platform, to ensure that this Low-Code Platform supports Systems Thinking via the enterprise Digital Thread. He has a BS in Civil Engineering from the Indian Institute of Technology in Madras, India, and an MS in Structural Engineering and Computer Graphics from Cornell University.
Technical session
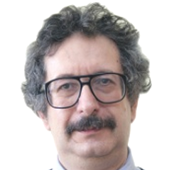
PSRE Co (NTP Truboprovod) | Leonid Korelstein
Centrifugal pump simulation during waterhammer analysis
The problem of centrifugal pump behaviour simulation during transient piping flow analysis is discussed. Implementation of 4-quadrant pump simulation on the base of Suter curves in PASS/HYDROSYSTEM software is described. Different related difficulties (lack of data from vendors on Suter curves and pump and motor parameters, merging of Sutor curves with real pump curves, role of damping/friction in the model) are addressed. Examples of calculation are given.
Curriculum
Graduated from Moscow Oil and Gas University in 1983, Applied Mathematics Master thesis
PhD Thesis in Mechanics and Mathematics in 1988 in Institute for Problems in Mechanics of Russian Academy of Science
More than 35 year experience in piping systems design and analysis: VP on Research & Development in Piping Systems Research & Engineering Co; responsible for PASS Analysis and Design software development, marketing and usage
Product Manager of PASS Process Engineering Suite software family
Associate Professor in Mendeleev University of Chemical technology of Russia, teaching Chemical Engineering students for Plant design and Plant design software
Active member of American Institute of Chemical Engineers, DIERS and European DUG
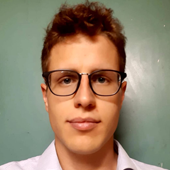
ZECO S.r.l. | Riccardo Orso
CFD analysis and optimization of a Kaplan turbine Draft Tube
The goal of the study is to obtain a geometry that reduces investment costs and increase overall machine efficiency. In the present study, an optimization study of the Kaplan draft tube was conducted. A CFD model for the complete turbine was developed and validated; an optimization was performed using a design of experiments technique. A selection of optimized geometries was subsequently post-checked using the validated model of the entire turbine.
Curriculum
Riccardo Orso is an engineer at ZECO S.r.l., Fara Vicentino, Italy which manufactures hydraulic turbines. He is a mechanical designer with some R&D activities. His educational background includes a Master degree at University of Padua, in Mechanical Engineering in July 2019, specialization in machine thermo fluid dynamics. He started his working career in 2016 with some mechanical design activities. From May 2019 he works in ZECO S.r.l., with different tasks, including CFD analysis and mechanical design of the hydraulic turbine components.
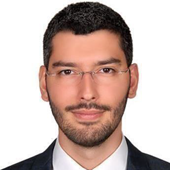
Bosch Thermotechnology | Fatih Tolga Özdemir
Experimental Verification of Drop Test Simulations of Combi Boiler
Experimental analyzes such as drop test, vibration and stack test are performed to determine the durability of products such as white goods, electronic devices and combi boilers to the loads exposed to transport conditions. However, at this point, numerical analysis is needed in order to keep the number of high-cost device drop tests to a minimum while managing the design processes. In this study, it is aimed to verify the numerical analysis method, which determines the dynamic deformation behavior of the combi boiler and its packaging system in the drop test, with experimental methods. In this context, numerical models were created and analyzed for situations where the appliance hits the ground in vertical and horizontal orientations. The drop velocities in these analyzes are calculated by reference to the drop heights included in Bosch's internal standards. As a continuation of the study, a high-speed camera was used in numerical analysis to determine the angle and duration of the appliance hitting the ground. In addition, measurements were performed using acceleration sensors in experimental tests to verify the acceleration-time profiles read from different points of the appliance as a result of numerical analysis. A good agreement has been observed between the acceleration profiles obtained from numerical analysis and experimental tests.
Curriculum
Fatih Tolga Özdemir was born on 15 April 1994 in Izmir, TURKEY. He received his BSc degree from the Department of Mechanical Engineering of IKCU. Mr.Özdemir is currently doing MSc in the Department of Mechanical Engineering of IKCU under the supervision of Prof.Dr.Mehmet ÇEVİK. At the same time, he is working as a Test and Simulation Engineer in the Research and Development Center of Bosch Thermotechnology.
CADFEM CIS | Oleg Zolotarev
Digital twin technology in the mining industry: Digital twin of a grinding mill
Mining industry companies implement digital twin technology to achieve higher efficiency of equipment and improve online monitoring of every its pieces. Advanced approaches use coupling DEM-simulation (Discrete Element Method), IIoT and predictive analytics. Our mill demo facility has been created to demonstrate related equipment, system architecture and user interface, which help to achieve higher efficiency of mill system as it works in real time.
Curriculum
In 2000 graduated with honors from the Navoi Industrial College with a degree in Operation and Repair of Mining Electromechanical Equipment and Automatic Systems. Completed an internship of the Navoi Mining and Metallurgical Combinat at the Muruntau mine.
In 2006 graduated from Moscow State Mining Universitywith a degree in Administration and informatics in technical systems.
In 2006 He began his professional career as a software engineer and worked his way up to the technical director of an engineering company. He has experience in the oil and gas, mining, cement and pharmaceutical industries, participated in large industrial integration projects. As part of his project activities, he collaborated with various local and international suppliers of automation software and hardware.
Since 2019, he has been working at Digital Transformation Factory. Responsible for technical development of the company and expansion of the range of products for various industries.
SVS FEM s.r.o. | Petr Konas
A parameter less shape optimization process allows to extend fatigue life of structural parts subjected to thermal fatigue
There are varieties of structural parts such as exhaust runner, turbo housing, valves, which are subjected to cyclic thermal stresses. Fatigue is one of the major concerns and hot spot mitigation is a paramount to get a good design. The need for tools capable of helping the designer in the definition of the optimal shape is still very high because the established approach usually requires the computation of sensitivity and a strong integration with the structural solver is required.
In this study we propose an approach that is based on the biological growth method and we adopt advanced stress results, as the cumulative plasticity, to drive the shape. The method is local and based on the structural solver results only. The surfaces of the part are reshaped, keeping the same solid mesh attached, by means of RBF mesh morphing.
The implementation adopted is based on Ansys Mechanical and its companion extension RBF Morph. The approach is demonstrated on a complex part, a valve, showing how a significant reduction of the hot spot stress level is achieved acting on the complete thermos-structural workflow used for baseline fatigue assessment.
Curriculum
Petr Konas, PhD in Technology of Wood Processing, is a specialist in Mathematical and multi-physical modeling of material and its properties with emphasis on biological ones. After an academic career at Mendel University in Brno started in 2001, he joined SVS FEM s.r.o. company in 2011 where he is now the Head of R&D. Petr is responsible for leading and providing development, research and code customization in multi-physical tasks for many industrial fields across all products of Ansys. Petr is a member of the Steering Committee for Eastern Europe at NAFEMS.